How does vacuum coating work?
Vacuum coating is a sustainable alternative to other coating techniques because it employs a 100% solid UV product, which is also more stable than polyurethane o polyester-based lacquers over time. It avoids contact between the application head and the substrate for clean, single-pass processing of 100% UV acrylic paint. Depositing up to 140 g/sqm this technique also helps reduce the number of coating stages when applying a basecoat, thereby saving workshop floorspace and improving lead times as well as limiting the number of handling operations needed.
benefits
The benefits of vacuum coating technologies
We have pioneered vacuum coating as an application technique because it ensures a significant number of benefits:
Using a solid UV lacquer, vacuum coating delivers a ec-friendly, longer-lasting, high-quality finish.
Superb transfer efficiency reduces costs, shortens lead times and boosts production output.
Same technique for both leads to a perfect match and the absence of an ugly junction seam.
Depositing large lacquer quantities in a single pass and integrating sanding capabilities reduces coating stages and handling operations.
Some specific application areas and products finished with vacuum coating
APPLICATIONS

Panel edges

Acoustic foam panels
Focus On
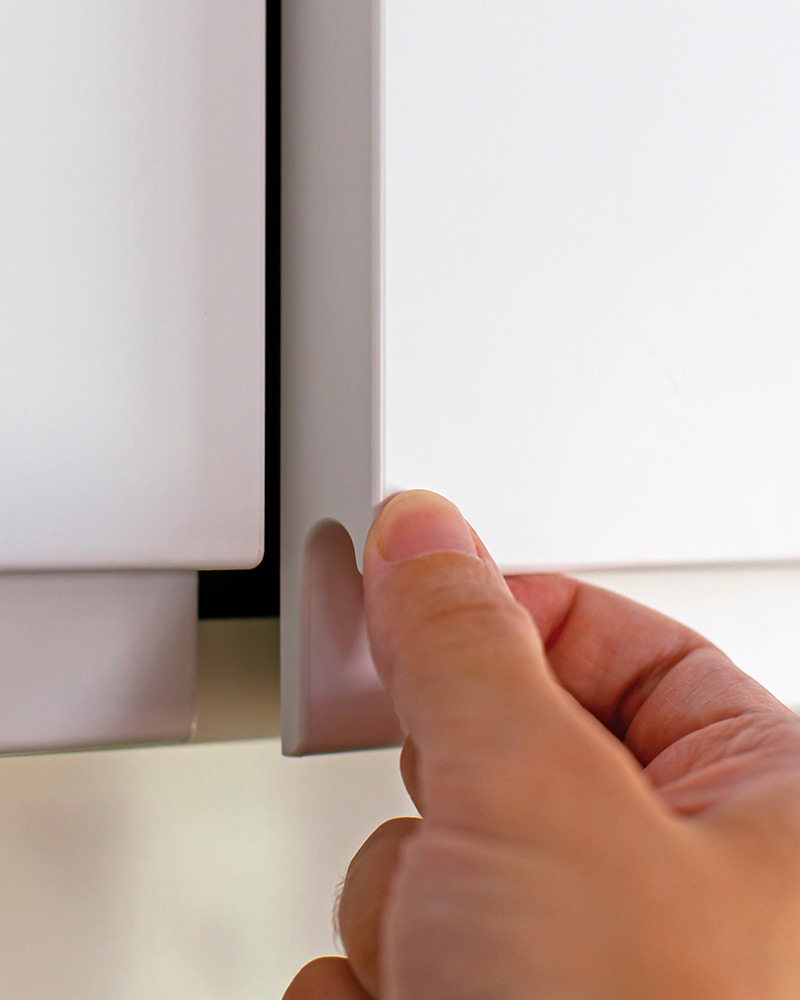
Perfect junction seams
Avoiding the ugly junction seam caused by the difference resulting from the coating techniques used for edge and panel surface is a priority for furniture manufacturers. By using vacuum coaters for both sections, this seam virtually disappears, leading to an improved panel finish, with a soft touch on its rounded edge.
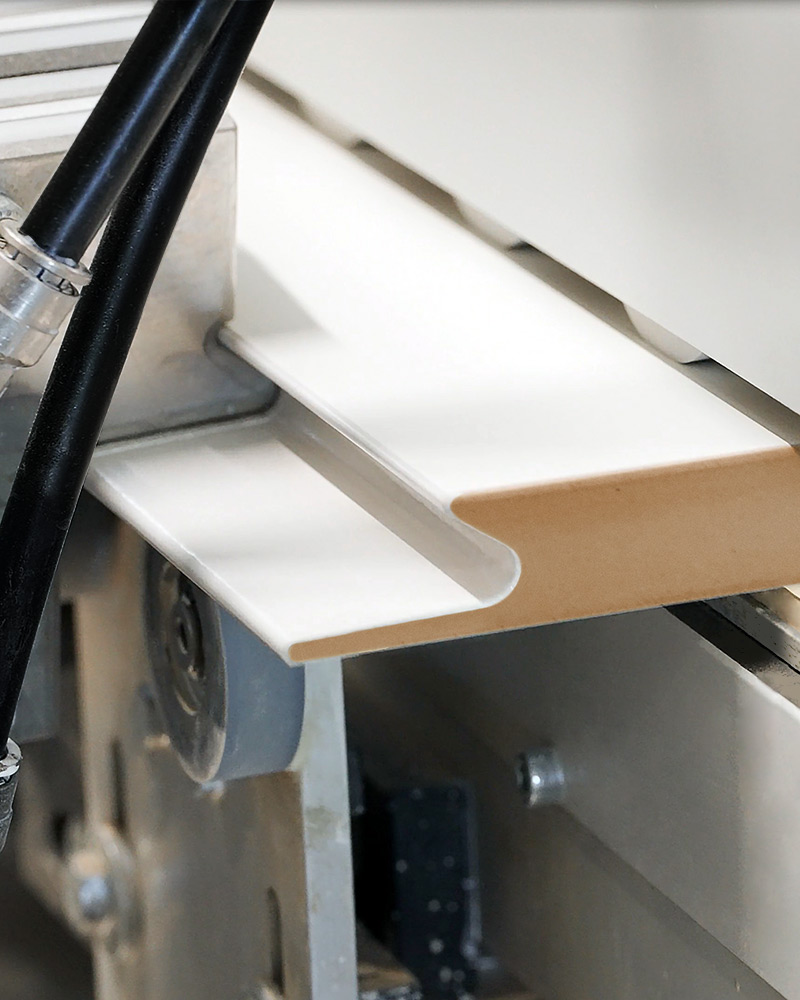
Double dispensing vacuum head
Recently launched, this new application head enables the Smartedge edge finishing machine to apply between 150 and 180 g/sqm. increasing capacity by approx. 50%. Moreover, a special blade helps the applied product to penetrate fibreboard parts ensuring maximum sealing performance.
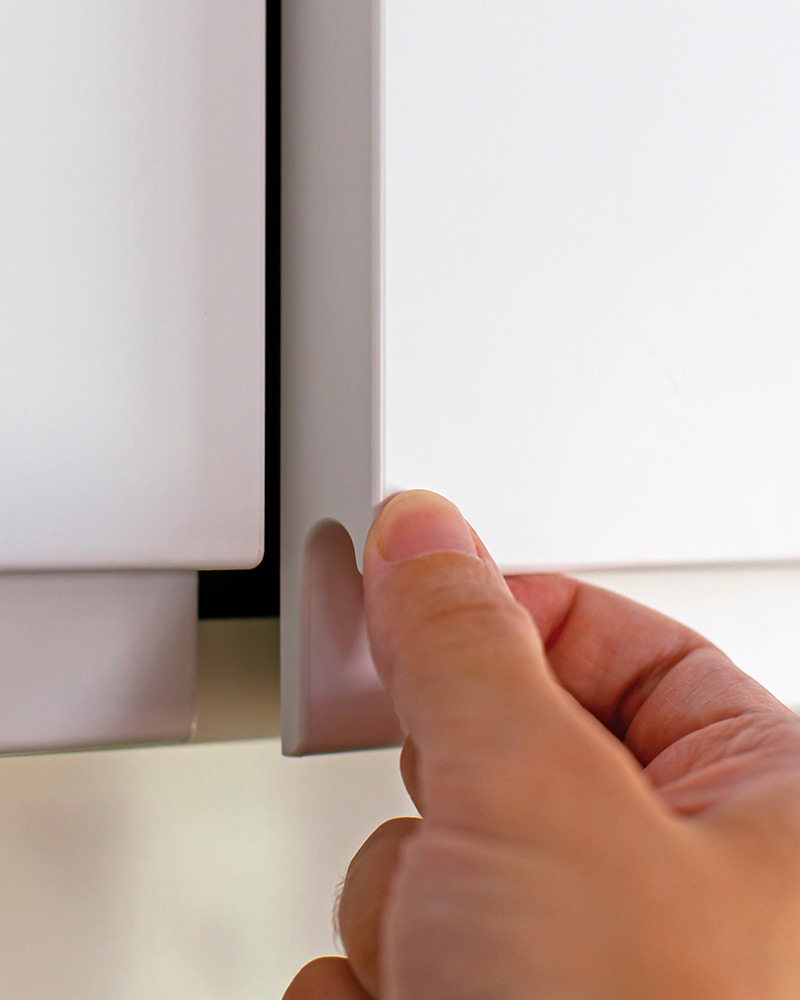
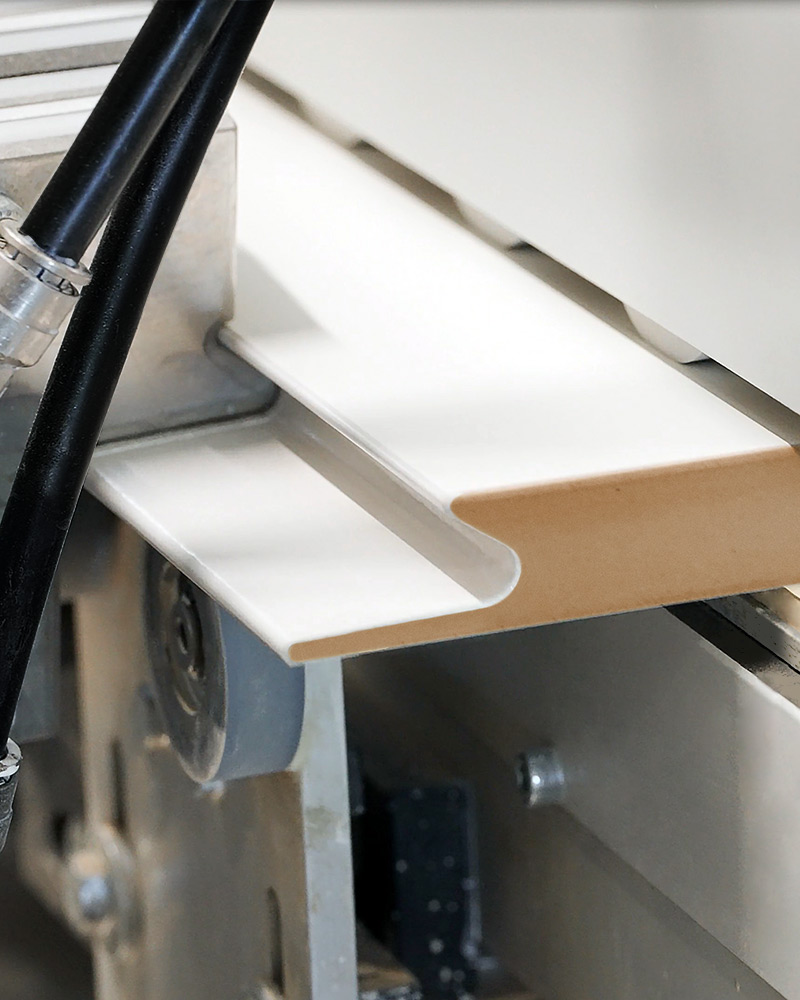
process
The vacuum coating process
Vacuum coating applies lacquer or a sealing agent in a single pass without the application head having any contact with the substrate (flat surface or edge). Transfer efficiency is almost 100%. Until recently, this technology was used for edges, coating, sealing or even waterproofing. Today, vacuum application solutions are a valid alternative for flat panels as well as edges.
Discover the vacuum coating equipment for surface coating applications as well as impregnation and sealing
Products
Case studies
Case study
WHITEPAPER
The most innovation finishing solutions
New finishing solutions: more effective, more productive and more competitive than those currently in use.
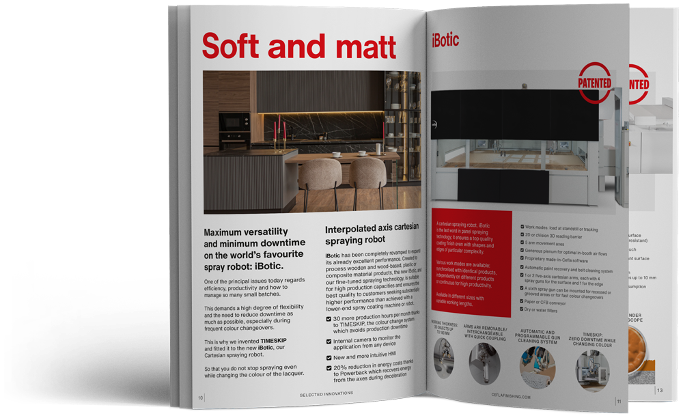
Learn More
MAGAZINE
The largest range of surface finishing solutions the world knows, developed in over sixty years serving the industry.
Tell us where you want to go and our finishing experts will help you get there.
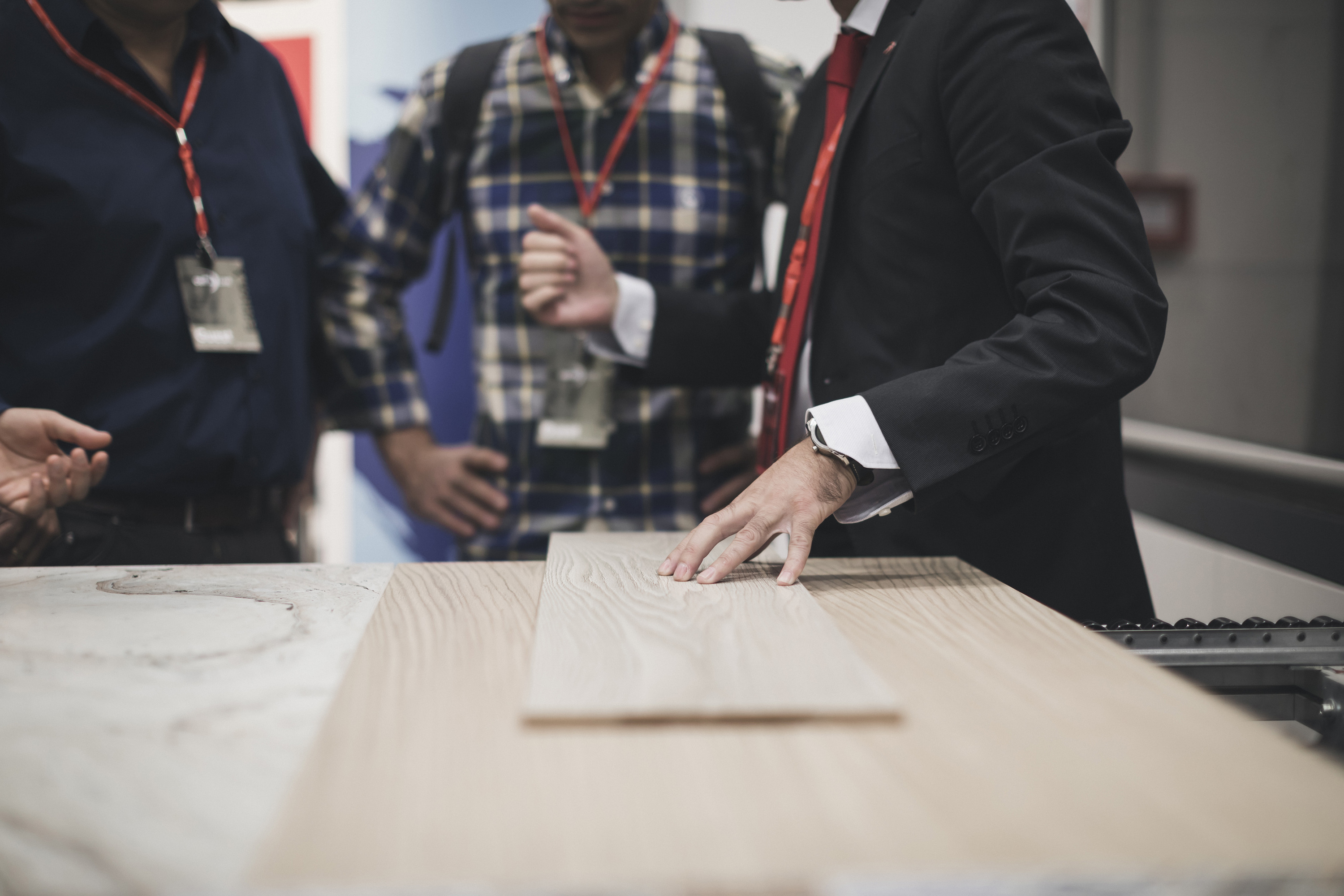
Connect
Frequently Asked Questions
Frequently Asked Questions
Cleaning times vary according to the size of the machine and the type of paint being used. Water-based paints require less time than viscous UV lacquers. On average, when changing profiles, it will take between 10 and 15 minutes. If you are also required to change colour, this will take up to 30 minutes.