What is meant by industrial paint or coating?
Rarely will you find an unfinished surface on any product. Most objects are coated with paints that can be water or solvent-based, UV acrylic, polyurethane, polyester and stains. These are applied mostly using automatic machines and in a precise order to ensure correct surface coating. Different stages of the process include coating with multiple layers, brushing and sanding, flash-off, matting, drying or curing. Application can be done using roller coating, spray coating, vacuum coating or curtain coating methods. Different product geometries require different coating solutions. Raised and flat panels will be processed on horizontal finishing lines, whereas 3D objects, window frames or doors can be painted using anthropomorphic robots; edges are finished on dedicated equipment.
Benefits
What are the benefits of industrial coating technologies?
Active in this industry since the 1960s, Cefla Finishing designs and manufactures the widest existing range of surface finishing solutions as integrated lines or tailor-made, stand-alone machines. Boasting 300 active patents and an installed base reaching around 15,000 machines worldwide, we develop coating equipment to maximise production efficiency and improve sustainability.
As an alternative to manual coating, automatic industrial coating ensures:
- Consistent quality: machines can be configured to provide the same quality finish day after day, week after week.
- Superior transfer efficiency: according to the selected technology, coating parameters can be set to ensure up to 100% transfer efficiency.
- Improved productivity: fewer handling operations and special systems built into the machines minimise downtime and reduce lead times.
- Overall sustainability: technologies, efficiency levels and automation strategies improve sustainability from an environmental, user-friendly and economic point of view.

In which industries are industrial paint solutions used?
Fields of application
Here is a selection of specific products that can be coated using industrial equipment
APPLICATIONS

External wall covering

Plastic components
How many different industrial coating techniques exist?
Each coating technique was developed to address specific situations, semi-finished or finished products. There is no better way to do it, but the most suitable way, and each technique has its pros and cons. Let’s take a look at the four most common technologies:
Ranging from simple machines to replace manual spray coating operations up to anthropomorphic robots that use software and 3D reading barriers to map out coating trajectories, spray coating solutions are extremely varied. The flexibility of spray guns able to reach almost all spraying angles makes this technique ideal for more complex shapes.
Discover moreRoller coating systems have evolved significantly and today’s solutions handle not only flat panel surfaces, but also raised panels presenting shallow grooves, such as cabinet doors. Excellent transfer efficiency makes them an ideal choice to reduce the number of coating stages on a finishing line.
Discover moreHighly sustainable and with transfer efficiency at almost 100%, this technology is perfect for both panel and edge coating operations, delivering identical results on each surface. Such close control over lacquer consumption makes this a technology in which there is very little waste of consumable products.
Discover moreSuitable for all coating types with different viscosities, and the ideal technology for polyurethane lacquers, curtain coaters provide high-quality finishes on flat surfaces, whenever large amounts of coating are required in a single application phase.
Discover some of the principal industrial coating machines
Machines
Case studies
Case study
Learn More
MAGAZINE
Experience spanning over 60 years, a network of finishing experts
Tell us where you want to go and our finishing experts will help you get there.
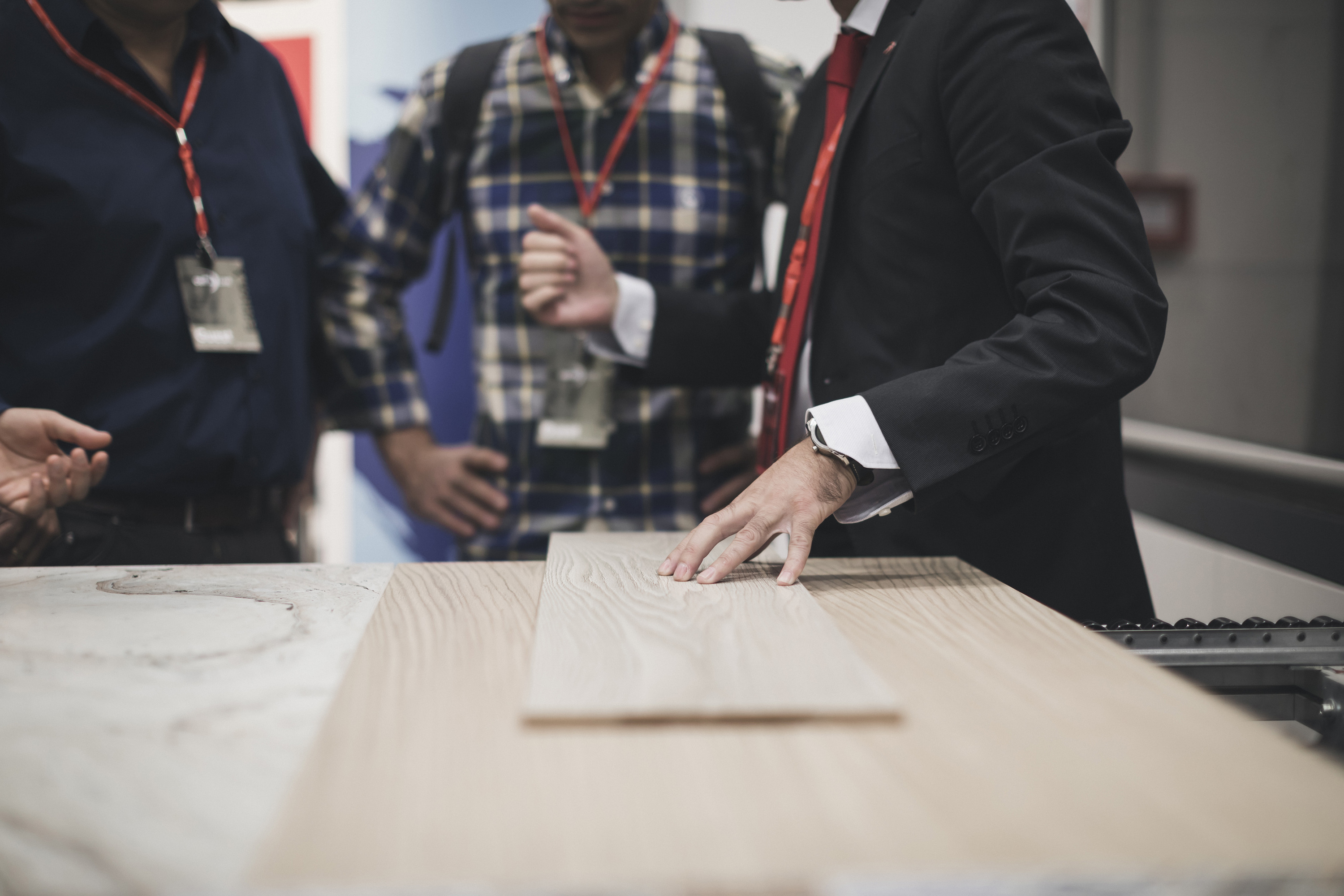
Connect
Frequently Asked Questions
Frequently Asked Questions
The quality of the paint finish is highly subjective. However, opacity and gloss, and obviously, the degree of application, can all be rated.
High flexibility in terms of output rate and choice of cycles/processes according to the line make-up.
Zero solvent emissions thanks to 95% use of products with high dry residue (UV) content.
Possibility of using the roller technique for any application on all flat surfaces.
Coating product consumption and consumption of solvents required for cleaning the machines in the coating line should certainly be considered and evaluated. Each step of the roller coating process must be monitored in terms of the quantity applied, for each individual machine. Quantities, in fact, may vary according to the type of substrate treated.