Automotive sector: component finishing trends
Climate change is forcing the mobility sector to take a sustainable approach. It is spurring the entire Automotive sector to abandon fossil fuels and invest in vehicles with lower environmental impact.
But what are the trends for car interiors, and vehicles in general? Manufacturers of interior vehicle components prioritise quality of finish, especially now that plastic is one of the most popular materials for a growing number of components. This, in fact, requires the increasingly rapid implementation of surface finishing and decoration technologies that can deliver both maximum quality and ultra-high production efficiency.
What Automotive finishing technologies are used for
When we think of industrial coating for the Automotive sector, the first thing that comes to mind is the bodywork. However, surface finishing, coating and decoration technologies are used in many areas, for example:
- coating of internal vehicle parts
- coating of external vehicle parts
- coating of wheels and wheel covers
- brake pad glue application
- application of sealing materials on metallic gaskets
- application of protective coating on lights
- number plate coating
- application of glue on interior leather/fabric linings
- mechanical component coating

Application of finishing technology in the Automotive industry
Technologies
Filds of application
Some specific application areas and finished products of the automotive industry
APPLICATIONS

Interior components

External components
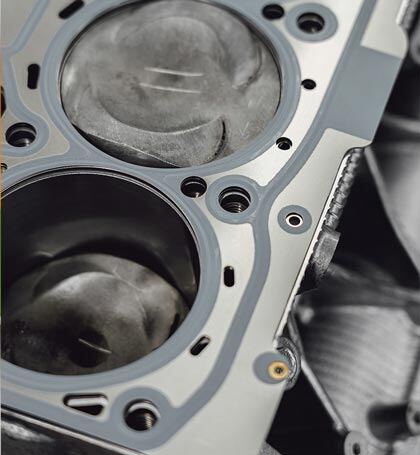
Seals
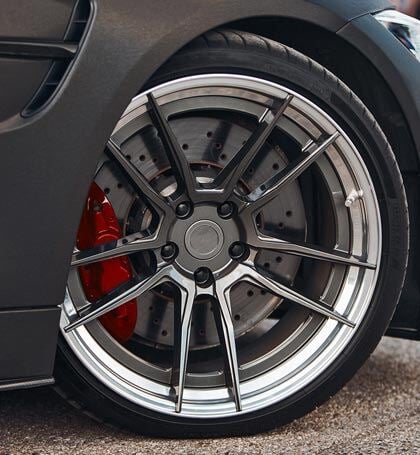
Mechanical parts

Clutches and brakes
Focus On
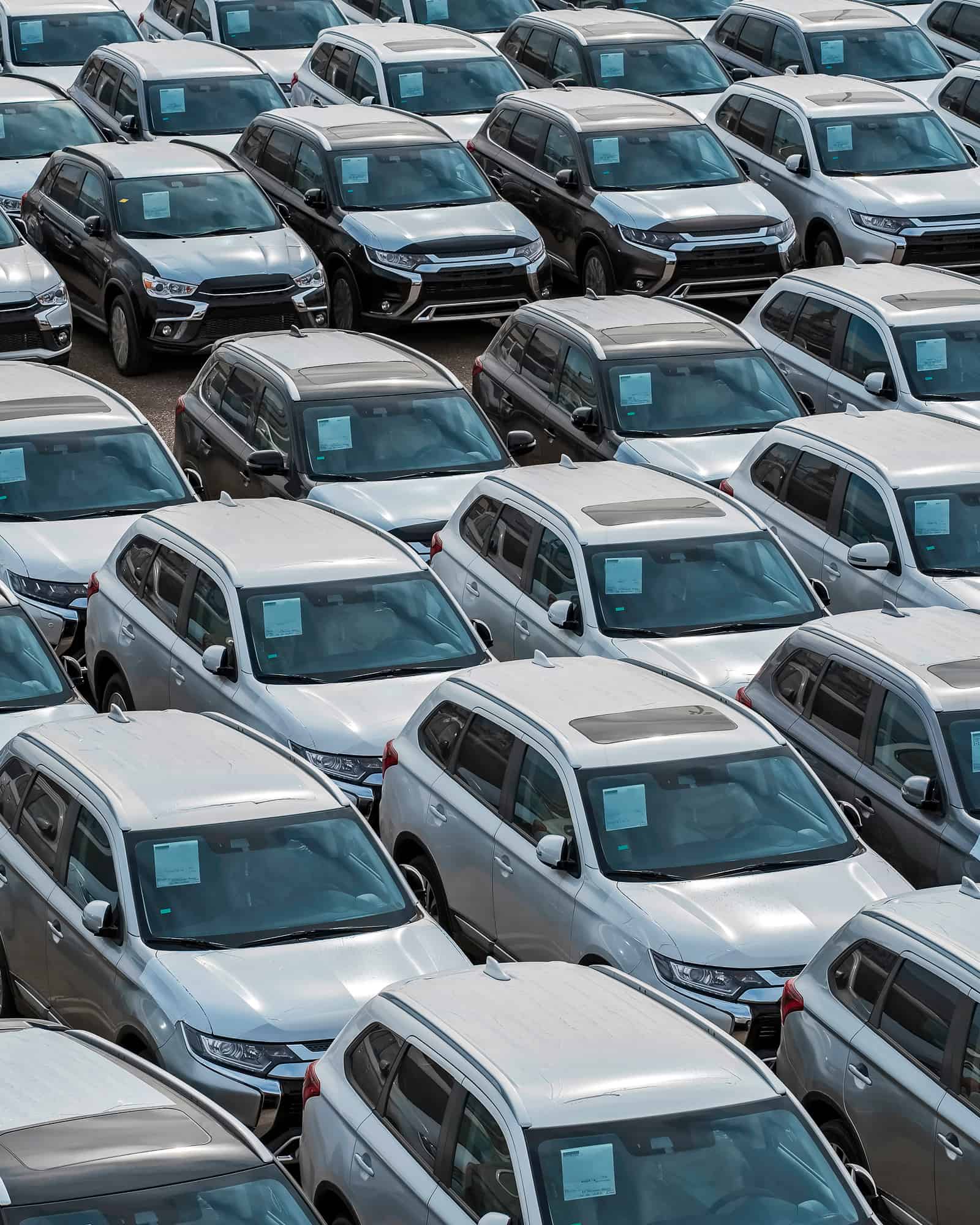
The response to market trends
For companies that work as TIER 1 or TIER 2, establishing good working relations with a car manufacturer is essential. To do so, guaranteeing the highest quality is not, on its own, enough: it’s also necessary to have a coating solution that ensures productivity and efficiency. This is where flatbed systems come into play.
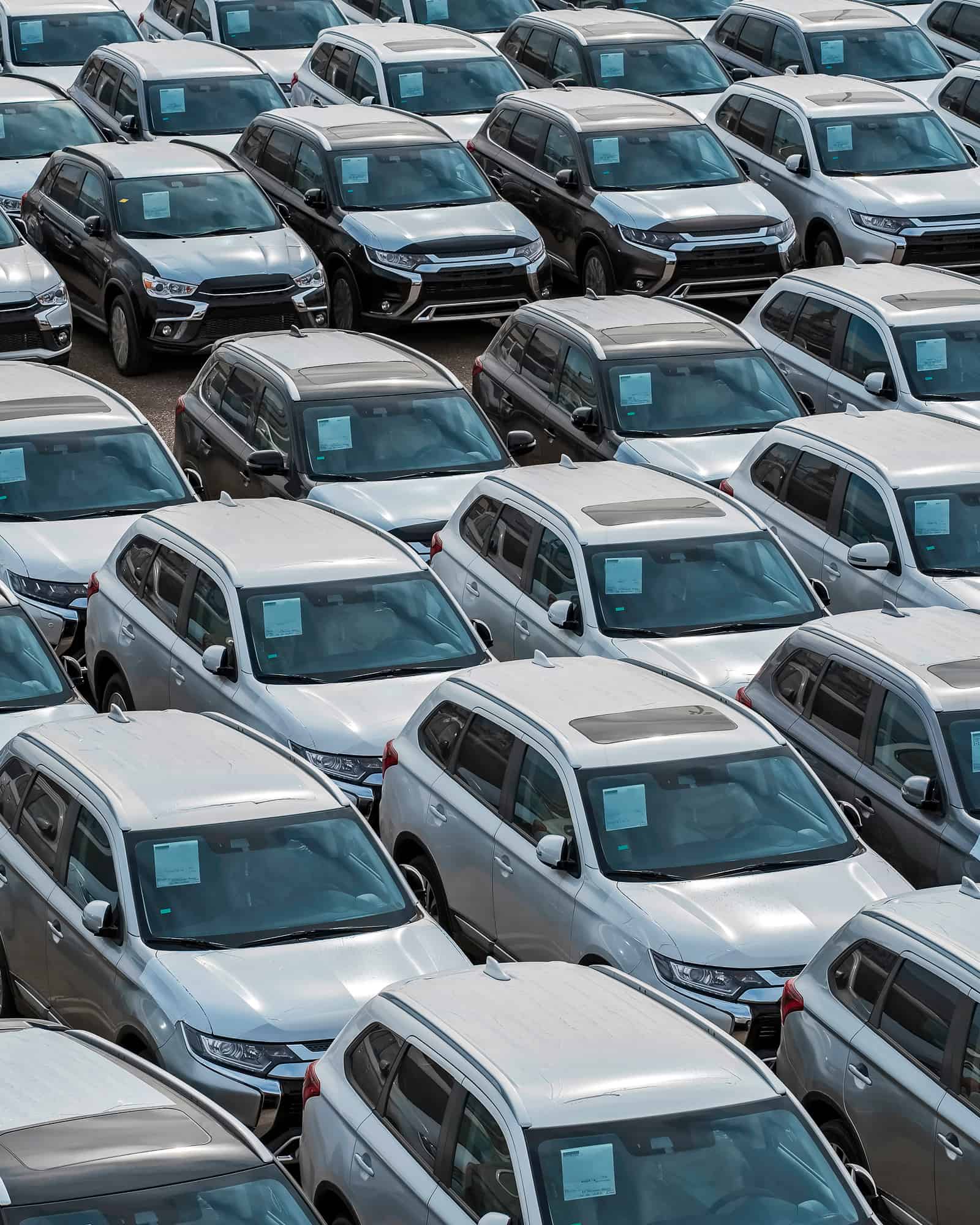
What are flatbed systems?
Flatbed systems replace the classic spray coating systems that use anthropomorphic robots that coat vertically, which is ideal for large components such as bumpers or spoilers.
And unlike traditional solutions, flatbed systems can also be used to manage smaller components: dashboards, central storage compartments, side mirrors and wheel hubs can thus be finished on a horizontal plane.
Flatbed systems: what are the stages of the process?
Let's look at the different stages of the coating process with a flatbed system. To do so, we’ll analyse the various steps on a Cefla Finishing Automotive line:
Prior to application, the automatic carbon dioxide snow cleaning function is enabled on the Mito oscillating spray coater to remove all surface dust and any contamination not eliminated by the manual cleaning performed during line loading.
For more complex parts, following deionization the components are recognised via a 3D digital reading barrier in the iBotic Cartesian spraying robot for the application of 20-25 microns of black PU pigment.
The component stays from 30 to 60 minutes in the Omnidry vertical oven.
A new coat of transparent coating is applied in the iBotic, if necessary with double polymerization at 70/80 g/m2. Omnidry comes into play again for 45 - 60 minutes at 70 °C and then everything moves into the UV oven (UV-R M2).
Advantages
Advantages of flatbed systems
Flatbed systems offer several advantages such as higher, more consistent quality and greater productivity.

Consistent quality

Optimised productivity
Learn about the machines that can help you create Automotive components
Machines
Case studies
Case study
Learn More
MAGAZINE
We’ve been innovating in the surface finish field for sixty years.
Experts sharing skills in all areas and all industries, Cefla Finishing is a hub of expertise, a trusted source and partner who can help you achieve your business objectives.
Tell us where you want to go and our finishing experts will help you get there.
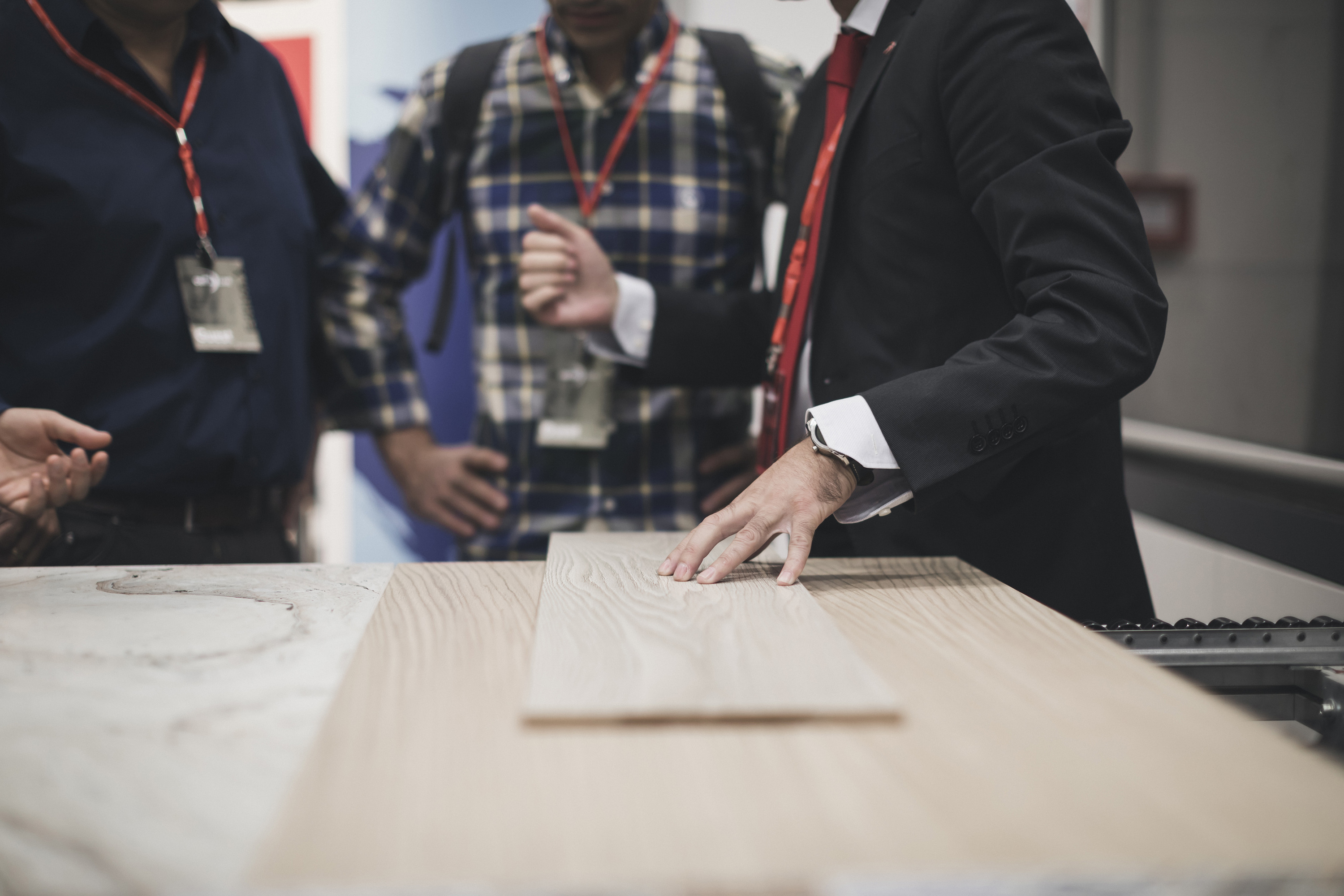
Connect
Frequently Asked Questions
Frequently Asked Questions
- That the coating must match the substrate material to ensure proper adhesion.
- That the piece being coated must be able to pass through the machines/systems.
- Anthropomorphic robot: more freedom, virtually unlimited 3-way movement. Unlimited spray gun positioning.
- Cartesian robot: less freedom, but can accelerate and move much faster. Limited spray gun positioning.