Offset and flexo printing
Offset and flexo printing are excellent techniques for long print runs as they keep costs down. However, on a market that is shifting towards increased customisation and minimal lead times, these traditional methods are no longer sufficient.
Unless you’re running large print volumes, offset and flexo work simply aren't cost-efficient. Small print runs are now frequent and the only way to make them profitable is to add an industrial digital printer to your printing equipment.
Focus On
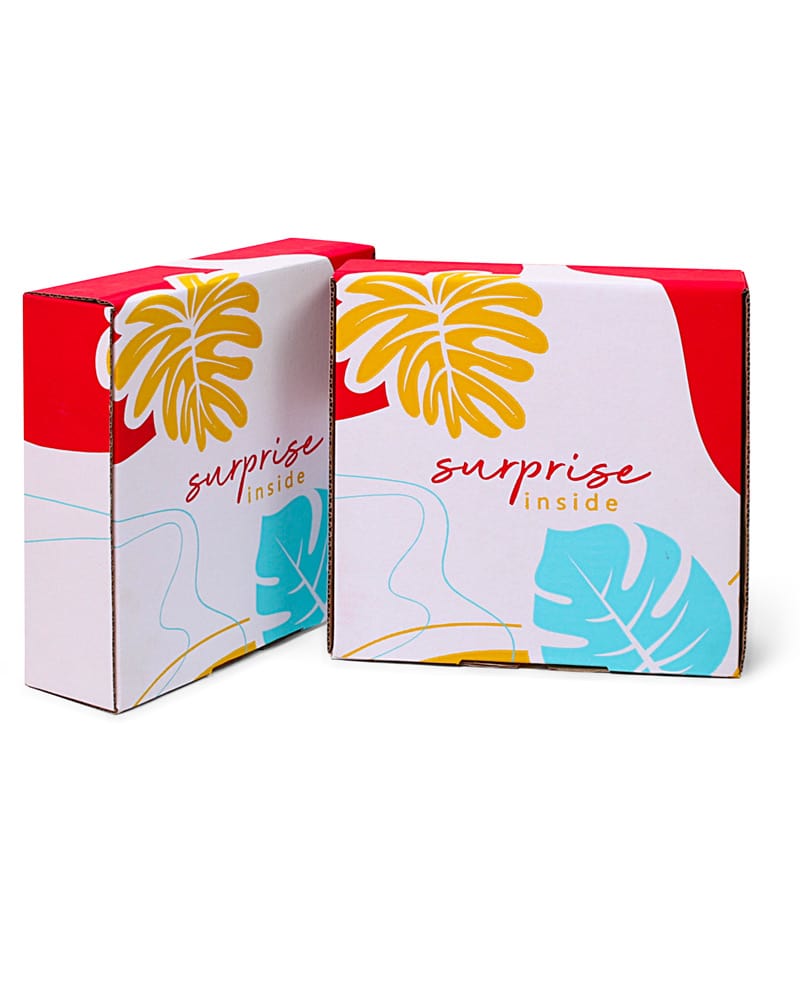
Digital printing for cardboard finishing
Cardboard is a sustainable material and for this reason many industries prefer it to plastic. This preference largely occurs in the packaging sector, and runs parallel to the increasing use of eco-sustainable products in the food, cosmetics and nutraceutical sectors. Some cardboard products - such as puzzles, disposable eyeglasses and place cards - also need to be decorated. Industrial digital printing is a technology that allows customisation of these products, even where volumes are limited, and without any proportional increase in costs.
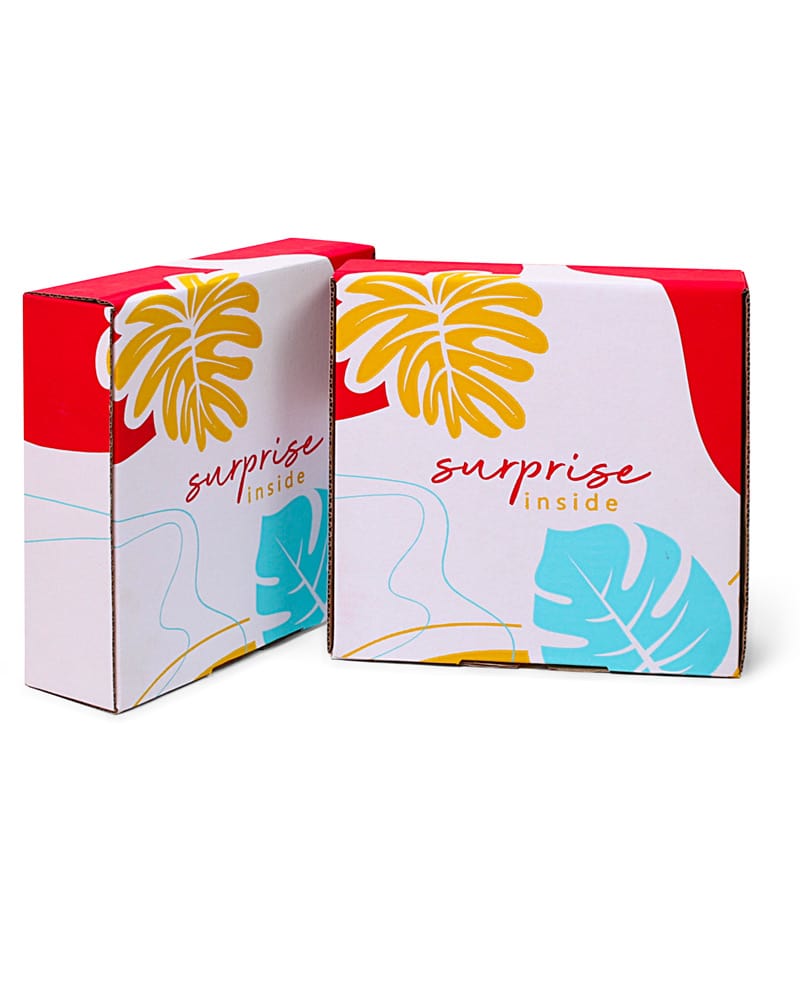
Benefits of digital printing
Turning cardboard into a box, a display or another form of packaging or any other product requires a number of processes. In addition to creasing, die-cutting and gluing, printing is also necessary. Industrial digital printing provides huge benefits when print runs are limited or customisation is required. Let’s take a look at these benefits:
4-colour (up to 7-colour) printing is possible with 2 degrees of nozzle density: 400 and 600 npi; resolution in the cardboard advancement direction from 800 to 1200 dpi depending on print speed.
Reproduce any digital or digitalised image (e.g. a puzzle) to print one-off data or content on cardboard displays or packaging.
Minimal set-up times, flexibility and the simplicity of the process that takes you from print file to printed product reduce time to market.
Industrial digital printers fit seamlessly into existing production lines regardless of the equipment upstream or downstream.
Thin sheets
Which finishing technologies are used especially for thin paper substrates?
Coating a thin paper substrate requires special attention due to the flimsiness of the material and its negligible thickness. Our technology has overcome this issue by counterposing an application roller which coats the upper surface of the paper sheet and a support roller which offers resistance to the application roller and prevents distortion of the sheet. A scraping system is provided under the machine - acting on the lower roller, to keep the substrate perfectly clean as it is fed through the roller coating machine.
Roll-to-Roll solutions are also possible for thin paper substrates and feature the same counterposed roller concept.
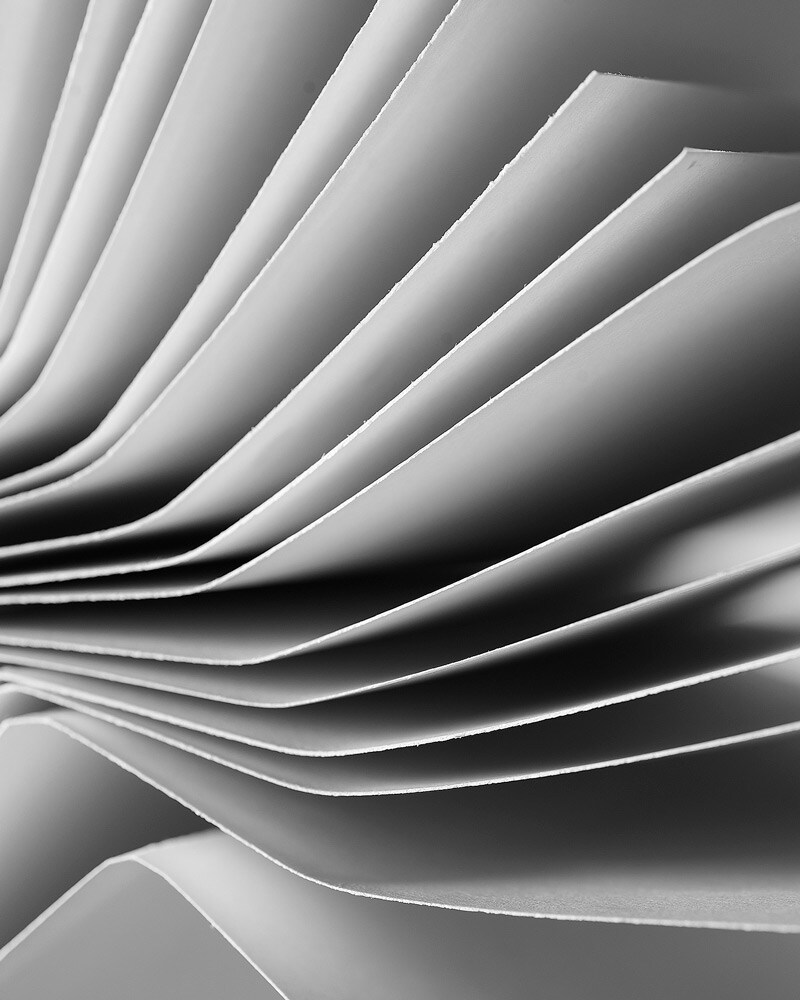
In which industries are cardboard finishing solutions used?
Sectors
Technologies
APPLICATION FIELDS
Learn about industrial machines for cardboard products
Machines
Case studies
Case study
WHITEPAPER
Industrial digital printing has unlimited potential
Discover all the potential effects that you can obtain on different substrates thanks to digital printing.
Downoload the White Paper
Learn More
MAGAZINE
We’ve been innovating in the surface finish field for sixty years.
Tell us where you want to go and our finishing experts will help you get there.
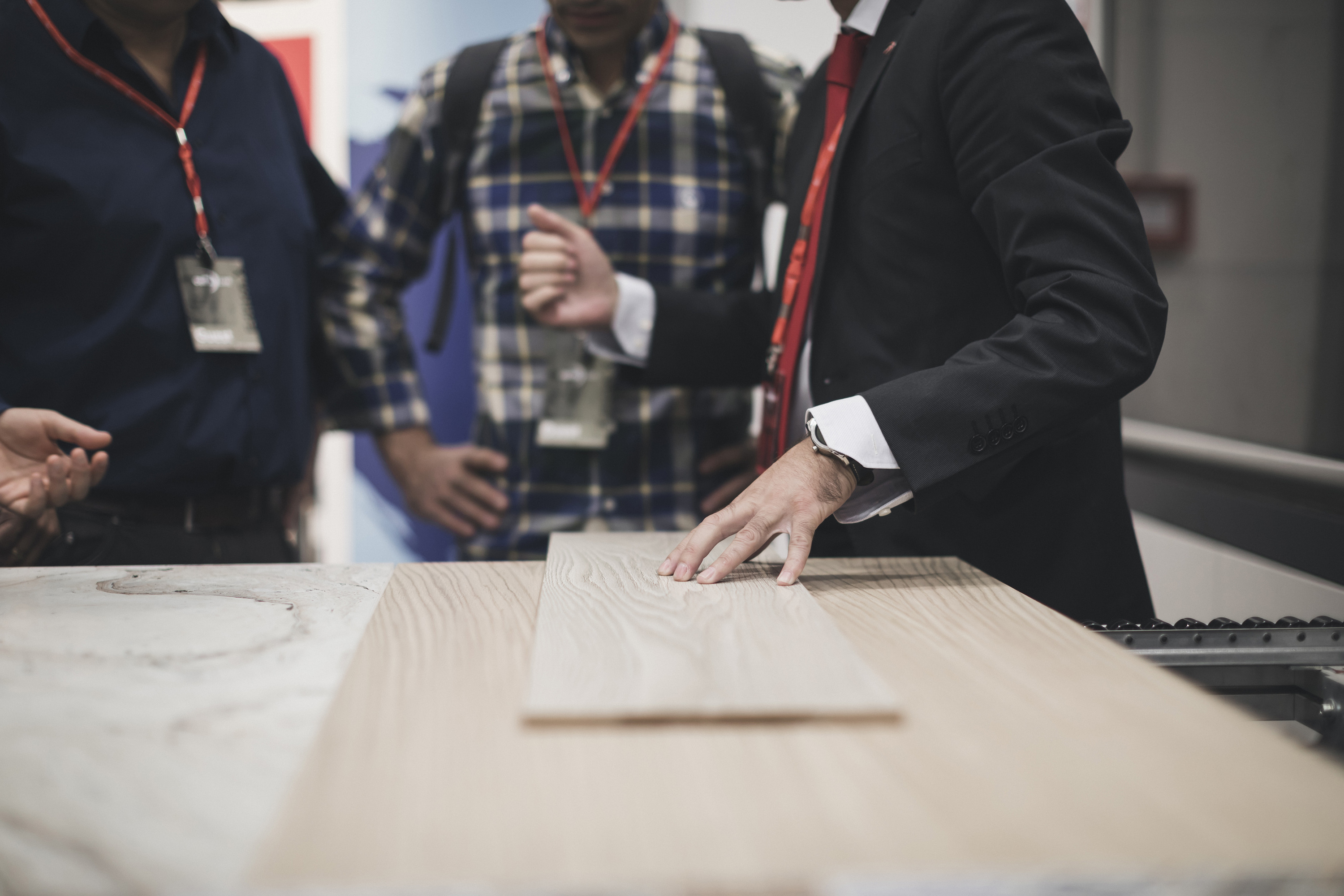
Connect
Frequently Asked Questions
Frequently Asked Questions
- Flexibility. It is simple to change from one design to the next as often as required.
- Unit cost is in no way connected to batch size.
- Quick response to fast-changing market demands and fashions.
- Very short lead time from the idea to the first sample.
- Ability to test countless variants, evaluate and pinpoint market trend instantly.
- Flooring
- Panel decoration
- Door decoration
- Edge-banding
- Fibre cement decoration
- Profiles
- etc.
Firstly, this does not mean “rapid prototyping”. It means creating a superficial 3D effect, a texture.
Yes, it is possible.
Achieved digitally on single-pass and multi-pass printers, there are 3 methods we advise to obtain different characteristics, all of which create a 3D effect. Depending on the end usage of the finished product, we would recommend one of these methods.
The first two methods are suitable for single-pass lines; both are "subtractive methods" (meaning that the "grooves" are obtained displacing/removing part of the high-resistant top-coat); the two methods differs for the way the grooves are obtained, one by displacing/rejecting the high-resistant top-coating, the other removing the high-resistant topcoating by brushing with suitable brushes the coating in the "to-be grooves" areas.
The third method is suitable for multi-pass machines and is an "additive method" (meaning that the "reliefs" are obtained by adding a specific ink, like in the additive manufacturing processes).
This can be achieved by implementing the following activities:
- Check hardware set-up daily: align the print heads, clean the nozzles.
- Check software set-up regularly: ensure nozzle compensation and shade uniformity across the conveyor.
- Ensure correct workflow and follow it strictly at all times: coating process control, colour profiling, image management, raster image processing (RIP).
- Define and perform Print Quality Assessment & Maintenance daily.
- Handling large volumes. This technique is not for mass production.
- Economies of scale. Unit cost does not drop in line with higher volumes.
- Learning curve. Many end-users are at the start of the learning curve and need to develop some skills and knowledge to exploit the technologies. We can support you.