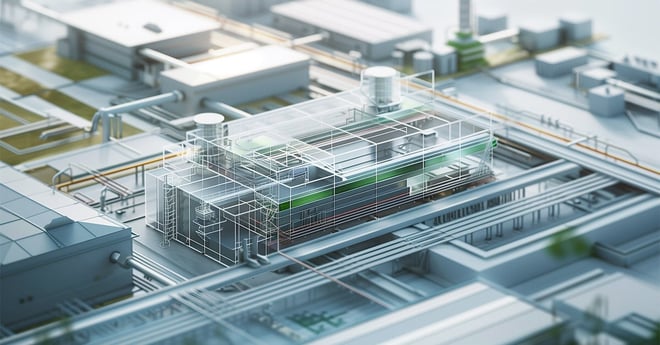
The reason is simple: a growing awareness of the impact energy production and consumption have on the environment and on climate change means that the most energy-intensive businesses will have to take the lead in implementing a series of solutions to drive through the required changes in society and the economy. But what’s the situation in Italy, and where is manufacturing headed overall in terms of industrial energy saving?
Let's start with some data gathered by the Confindustria Study Center: in 2022 industrial companies decreased gas consumption by 13.2% compared to the three-year average of 2019-2021. Electricity consumption also fell, by 5.6% (compared to 2021), resulting in a much larger reduction than that achieved by the Italian economic system as a whole (-1%).
What’s more, an analysis of electricity consumption in Italy shows that industry is by far the biggest user. As the Digital Energy Efficiency Report 2022 (published by the Energy & Strategy Observatory of Milan Politecnico) points out, 44.1% of national expenditure is absorbed by the industrial sector, with 39% of Italian electricity consumption attributed to manufacturing alone (2020 data).
The report highlights that in 2021 spending on industrial energy efficiency reached 2.2 billion euros, with 90% of investment involving hardware upgrades.
Things are, then, changing: but there’s still a long way to go. This article examines which steps can be taken today (and in which direction), mainly with a view to maximizing the efficiency of surface finishing processes, which are among the most energy-intensive.
Read also:
● Industrial Energy Efficiency: the key is in the finish
Energy saving challenges in the manufacturing industry
Let's begin with the challenges to be faced: the first concerns the high levels of capital investment needed to upgrade equipment and implement energy-efficient technologies. We then need to factor in the complexity of the production processes and the variety of equipment used, which can make it hard to identify the most effective consumption control/reduction solutions
Then there’s the issue of cultural and organisational change: implementing energy saving measures may require major modifications to operations and employees’ tasks; workers may express reluctance or even resistance to new measures. Last but not least, note the increasingly stringent regulations and standards, compliance with which often requires further cost and effort in addition to those already analysed.
What are the strategies for industrial energy saving?
In general, lower energy consumption per unit of product can be obtained via three strategies. These can be applied individually or in combination. Again, according to the Confindustria Study Center, these respectively involve:
- an increase in energy efficiency, with technology, plants and machines remaining equal
- a sector-based reorganisation of production, towards sectors of lower energy intensity
- a change in production technologies and/or plants and/or machinery.
On a purely practical level, manufacturing companies can generally reduce their energy consumption by, above all, adopting LED lighting in their plants, introducing high-efficiency motors and focusing on ‘smart’ energy management (e.g. by using their own photovoltaic and energy recovery systems).
More specifically, when it comes to finishing processes, it’s essential to access technologies and patents that allow manufacturers not only to reduce consumption but also stand out on international markets through the quality of their products and achieve ever-greater production flexibility. This is exactly what the Cefla Finishing range lets you do.
Industrial energy saving technologies and solutions
The Cefla Finishing portfolio of solutions, designed to help companies achieve their industrial energy saving goals, consists of three branches: automation and control, low-temperature drying systems and energy recovery systems. Let's look at these in more detail.
Automation and control
Optimising processes and consequently reducing energy consumption means implementing a series of automated operations that, on the one hand, minimise waste and, on the other, increase control over the efficiency of existing procedures.
In this context, small and medium-sized companies can reap the biggest rewards from the introduction of automated solutions like Prima Evo, an oscillating one- or two-arm spray coater, ideal for making the switch from manual to automatic spraying.
Low-temperature drying systems
As said, drying processes are a major contributor to high energy consumption in manufacturing companies. That’s why we need to start here if we want to substantially shrink the environmental footprint.
By adopting UV LED gelling and drying ovens made by Cefla Finishing, for example, it’s possible to reduce energy consumption by around 50%; this is because the LEDs that replace the traditional UV lamps are much more efficient. Furthermore, since these lamps are cold, substrate heating is limited, drastically reducing the number of rejects and the need for reprocessing; that means both energy savings and a reduction in the environmental impact of processing. Other sustainability enhancers include the absence of mercury - a pollutant not present in LED technology - and the fact that the production process involves zero ozone emissions.
Energy recovery systems
Last but not least, let’s look at the Power Back energy recovery systems that Cefla has implemented on its iBotic robotic spraying lines. Conceptually, the working principle is similar to the one that allows electric car motors to recover energy during braking, with the vehicle's wheels transferring kinetic energy to on-board systems. Similarly, the Cefla Finishing Power Back system enhances control of arm movement, ensuring less electrical ‘expenditure’ and, above all, retrieving energy during the machine deceleration phase.
What are the benefits of industrial energy saving?
Several tangible, measurable advantages can be obtained by implementing industrial energy saving strategies: manufacturers will naturally imagine the possibility of increasing margins while simultaneously becoming more competitive compared to those who have yet to take the same development path. Yet we should remember that reducing consumption also means reducing the carbon footprint: an excellent way of bolstering your reputation with partners, customers and end consumers.
Of course, the obstacle of the initial investment remains and this can be costly, especially for an SME. Luckily, today we can count on a range of incentives for investment in innovative technologies: tax relief, grants and subsidised financing linked to ESG goals now allow almost any organization to cope with an expense which, in any case, guarantees an extremely fast ROI.
Want to know how quickly in the specific case of your company? Contact a Cefla expert and visit the Cefla Finishing Lab to experience, first-hand, all the solutions and technologies that help reduce energy consumption in your finishing processes.