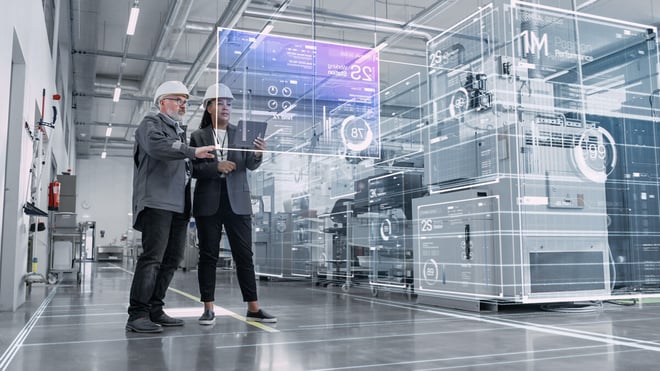
Types of industrial automation systems
In the coating sector, automation processes can be divided into two main families:
- Automation of the technological process (sanding, cleaning, application, drying)
- Automation of the line or the handling of the items to be coated (loading/unloading, overturning, conveying and transfer systems, etc.)
A further classification can be added to these two categories. Industrial automation can, in fact, be rigid or flexible. The former usually deals with process, assembly and verification tasks, while the second concerns control of materials and products (i.e. logistics and machines that are free to move). Then there’s the third way: programmable automation.
At present, Cefla Finishing is able to help manufacturing companies set up automated lines by providing internally developed machines and patented technologies to meet all their finishing requirements; while this does not directly include loading/unloading systems, the development of customised end-to-end solutions is ensured by close collaboration with highly qualified partners.
Before going into a detailed analysis of the advantages of industrial automation systems, let's focus for a moment on the opportunities offered by the market and the product ranges Cefla Finishing has developed for each one of them.
Rigid automation
Rigid automation systems are ideal for large-scale production with fixed operating sequences. These solutions are mainly used in the Packaging sector, especially the ‘pick and place’ sector.
Flexible automation
Flexible automation, instead, concerns highly configurable systems that are well suited to managing the diversified production scenarios that finishing and coating companies habitually manage.
In this area, Cefla provides comprehensive line automation solutions (cTracker, Smart thick, cViewer) that allow end customers to reconfigure the entire line easily and effectively to match the required type of processing.
Programmable automation
Last but not least, programmable automation involves the implementation of batch production systems, which require frequent reconfigurations.
This is a Cefla Finishing speciality: the machines designed to automate the finishing and coating processes control local set-up recipes that allow easy reconfiguration according to the type of product the customer wishes to finish.
For example, if the sprayers operate according to specific coating recipes, so too will the ovens during the different drying phases.
In essence, manufacturers can - based on the type of product to be finished - set and save all the machine set-up parameters to guarantee optimal final results, with the advantage of being able to recall each setting to speed up line reconfiguration as production lots gradually change.
READ ALSO:
Cefla technologies that deliver industrial energy savings
Industrial Energy Efficiency: the key is in the finish
Advantages of industrial automation
Automation provides the finishing sector with a host of benefits. First of all, it makes production safer. Where work involves dangerous materials or is physically taxing, the toughest tasks can be performed by robots, exposing workers to less risk.
However, as everyone knows, the main reason why manufacturers invest in automation is that these technologies reduce operating costs significantly. A well-designed system that automates coating and finishing processes reduces downtime, speeds up deliveries and minimises unexpected breakdowns/stops in production and logistics processes.
Nothing clarifies the concept better than a practical example: Cefla Finishing sprayers are, for instance, equipped with vision and air intake systems that reduce the amount of wasted lacquer. Customers can also take advantage of further mechanisms that retrieve the portion of product not actually applied on the piece during spraying and, where possible, reuse it to perfect the work. These solutions, then, increase coating uniformity and consistency, improving final results and generating significant savings by reducing product consumption and waste disposal costs. Furthermore, automating such tasks leads to clearly better plant safety by preventing workers from coming into contact with potentially harmful substances.
Workers’ quality of life also benefits from greater personal satisfaction: introducing industrial automation systems lets companies free their personnel from monotonous, repetitive tasks and employ them in more strategic or higher-added-value activities.
Key technologies in industrial automation
To deliver the above-illustrated advantages, it’s essential to properly orchestrate all the technological components onto which industrial automation systems are grafted. As mentioned, in the field it will be necessary to leverage IIoT (Industrial Internet of Things) solutions that allow real-time collection and distribution of data from the production lines: data essential for enabling monitoring and control via human-machine interfaces (HMIs) and more complex solutions such as SCADAs.
Cefla Finishing has developed a machine pool that’s controlled by PLC and HMI. This lets customers interconnect an entire line or individual machines with IoT systems. Where required, it’s also possible to export data directly to the cloud.
Practical applications in industry
More specifically, the aforementioned cTracker offers the best solution on the market for automatic control of both the technological process and line automation. The solution lets you programme batch processing cycles - such as colours, number of passes and line speed - directly from the office. Thanks to an internally developed algorithm, cTracker collects information on batches, simplifying machine settings to match production needs. This happens without having to empty or stop the line at each batch changeover and without having to use physical on-piece tracking systems.
A concrete example is provided by our client Finver: thanks to the finishing line we implemented, it is possible to anticipate colour changes, resulting in an annual savings of 25,000€ on paint costs while also reducing disposal costs.
To conclude, with today’s state-of-the art technologies, the opportunities that industrial automation systems offer the finishing sector are virtually endless. The best way to fully understand how your company can benefit from the industrial automation systems developed by Cefla Finishing? Simply visit us and see the potential of our technology for yourself. Just contact us and ask one of our experts for advice!
LOOKING FOR THE IDEAL COATING LINE SOLUTION?