Flooring is one of the most demanding applications in terms of surface enhancement. Industrial digital printing technologies address issues such as quality, customisation and resistance to foot traffic in a highly satisfactory manner. In particular, close attention needs to be paid to the third issue, which is regulated by European standards, as well as international standards.
Recap of the process
Industrial digital printing as a solution for flooring involves a fairly articulated process. These are the steps that need to be considered:- Sealing (in the case of MDF) or Adhesion Promoting (for plastic substrates)
- White layers
- Digital Printing
- Wearing layer
- Textured layer
- Finishing layer
Innate flexibility and a time-saver
One key advantage of this technology is the outstanding flexibility you benefit from in relation to changes in market trends and fashions. Even when running small batches that demand frequent set-up operations, time is saved thanks to fast line set-up, plus minimal stock of semi-finished goods.
Durability as a determining factor
Foot traffic resistance is one of the critical factors due to surface deterioration, especially in areas such as hotel foyers, corridors, offices, showrooms, schools and retail environments where there is a constant flow of people.Flooring durability is these cases is regulated by the EN 15468 and EN 13329 standards governing laminate floor coverings. In each case, Cefla Finishing has accomplished the required tests reaching AC4 and AC5 (Abrasion Criteria) standards for its digitally printed laminates. Ink type determines the aesthetic qualities of a floor covering, sometimes also with regards to resistance over time. Flooring is mainly a market of products for interior use; there is nonetheless a specific kind of flooring especially for exterior use: decking.
Whereas organic pigmented inks tend to fade, in the outside, in the first 2 years of exposure to natural lighting if no special UV-protection coatings are applied on top of the decoration layer, inorganic inks are also available with pigments made out of metal oxides, that are hardly affected by light for between 10 and 15 years. While organic pigmented inks, with their superior colour gamut (colour range), are perfect for interior use, as well as some exterior use when properly protected against UV weathering, the inorganic pigmented inks are an interesting choice for exterior use, as in the case of decking, reducing the need for a special UV-filtering top-coat.

Discover the machinery that allows you to achieve these results.
Machines
WHITEPAPER
How to optimise roller coating technologies for a growing variety of products and substrates

Do you want more information?
Please contact one of our experts.
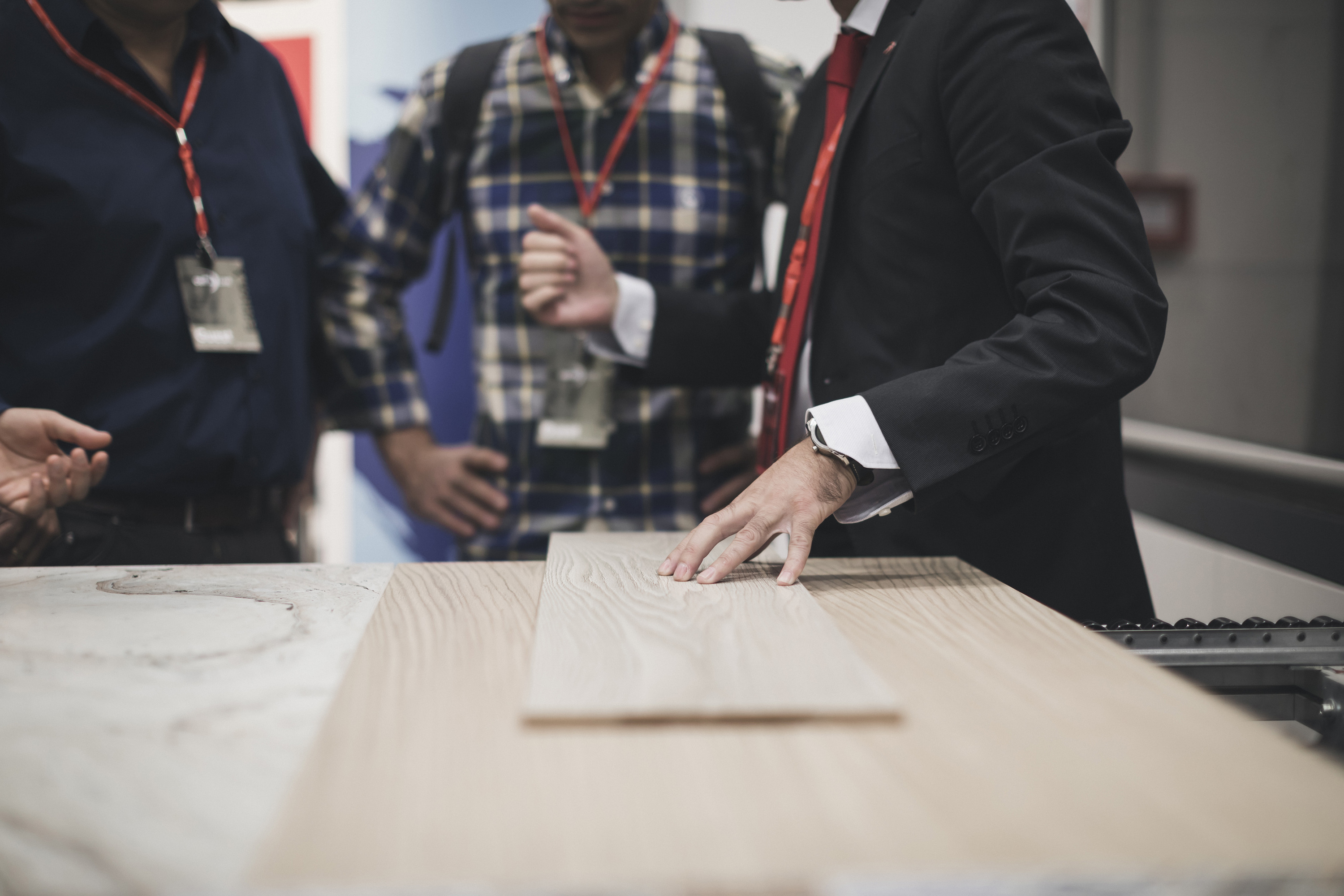
Connect