Fridays for Finishing – a look at HIB’s 20% gain in productivity
Project Data
Customer:
Third party automotive components producer
Country:
Germany
Media Video:
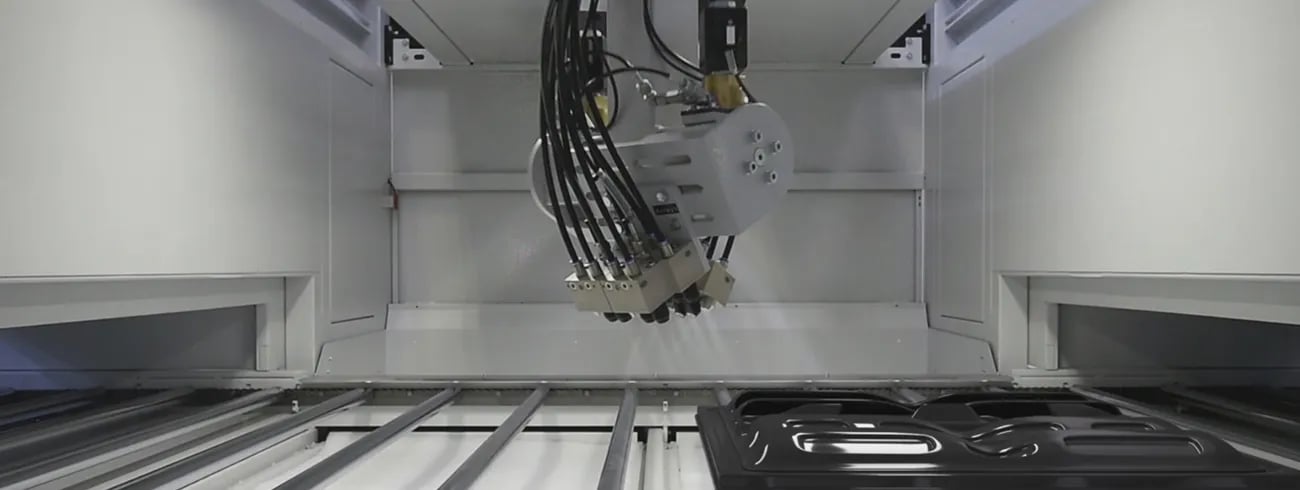
Tight production schedules, maximum productivity, flexibility. It’s all about fitting more finished parts into less finishing time. So if Fridays were free to handle other customers or other jobs, how would you feel?
One of our customers who supplies dashboards and central console blocks to a leading European car manufacturer is now covering the full weekly volume demanded in 4 days instead of 5. We helped make this possible with our technologies.
Predominantly “piano black” which is a high-quality glossy finish, but also matt silver in smaller numbers, the parts are processed on a Mito equipped with CO2 snow cleaning capability to prepare the surface, followed by an iBotic twin-arm Cartesian spraying robot.
Processing on a flat bed line with a working width of 1600 mm, the components are fixed to a frame two at a time on the non-stop conveyor made of steel strips, enabling high productivity. cTracker software allows operators to track pieces on the line, recording data to analyse productivity and to implement production changeovers without emptying the line. Flexibility is one of the key benefits of the flat bed line, allowing the customer to exploit the full conveyor width and load according to needs. Cefla Finishing technologies have boosted productivity by 20% enabling the customer to satisfy the required volumes in the first 4 days of the week. Achieving such a degree of productivity has also meant a fast return on investment.
Now comes the question about what to do on Fridays.