What is meant by the industrial surface finishing of metal substrates?
Metal substrates undergo a finishing process in most cases, yet only a few of these can be considered as a coating process, either using paint or powder. Other finishing processes for metal include a wide range of techniques which may even alter the molecular structure of the substrate. Applied to enhance the surface of a product made of metal - for example: plating, anodizing, electropolishing – coatings are also used to embellish the surface and protect it from weathering.
Processes
Why is metal coating important for certain industrial sectors?
The construction industry is one sector in which metal substrates are quite common, usually in applications for use externally, such as windows, doors, sidings or even decorative panels. Metal piping is another product requiring a finishing process, found in general industrial applications. Each substrate, either due to its shape or due to its final destination, will need to undergo a different finishing process. These processes include:
- Coating: mostly performed using spray coating technologies and equipment, roller coating and vacuum coating techniques are also used for specific products.
- Wrapping: aluminium profiles that may be a part of a window frame can be wrapped on high-tech, automatic machinery to improve their look and feel.
- Industrial digital printing: enables attractive personalisation of the surface, and both large volumes as well as batch one assignments.
- Drying: following most coating processes, a drying stage is required to maintain constant line output.

In which industries are metal finishing solutions used?
Integrated finishing lines for metal elements can be found in diverse sectors and for several different products:
APPLICATION FIELDS
Here is a selection of metal finished specific products
APPLICATIONS

Architectural structures

External components

Profiles and structural metalwork

Coils

Tubes

Clutches and brakes
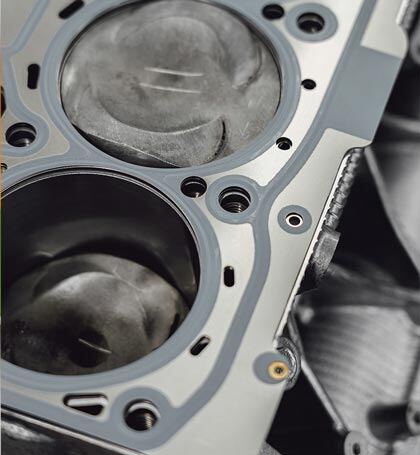
Seals

Aircraft structural parts

Interior components
Metal finishing technologies and processes
Different finishing technologies are used for metal substrates according to the production volumes as well as the geometries of the end product. The following are a selection of the most common processes found in different industries:
A flexible solution which ensures coating consistency applying lacquer to all sides of a 3D product. Spray coating is accomplished on flatbed lines or overhead lines with special spraying robots.
Discover moreFor excellent transfer efficiency, this coating technique can be used on flat panels and panels with shallow grooves, performed on specially equipped roller coaters. For ultra-high-gloss surface finishing, a Laser roller is the perfect solution.
Discover moreHigh-quality coating with almost 100% transfer efficiency using 100% UV acrylic lacquers for flat surfaces and edges, especially if the edge needs to match perfectly with the surface finish applied to the panel.
Discover moreThe ideal solution for customisation or batch one requirements, this technology transforms a unique digital image into a printed decoration and can be integrated into lines using other coating technologies.
Discover morePart of automatic equipment providing solutions for a complete process including an adhesive coater unit, wrapping is performed on profiles and window frames in aluminium.
Discover moreDifferent ovens implementing IR or UV technologies are available to dry the lacquers used to coat the metal substrate.
Discover moreThin sheets
Which finishing technologies are used for thin metal or graphite substrates?
Our roller coating equipment can be tailored to coat thin metal sheets, and according to where the final product is used, will be handled in an appropriate environment if this needs to be dust-free.
While coating thin metal sheets, the machine works with two counter-facing rollers, one above to apply the lacquer and one below acting as a support and featuring a cleaning device to keep the lower surface lacquer-free.
Metal engine head gaskets can be coated this way or on specially designed spray coating equipment to ensure a perfect, closely controlled surface finish.

Our technologies have been developed to optimise the industrial finishing of metal substrates
Machines
Case studies
Case study
Learn More
MAGAZINE
We’ve been innovating in the surface finish field for sixty years.
Tell us where you want to go and our finishing experts will help you get there.
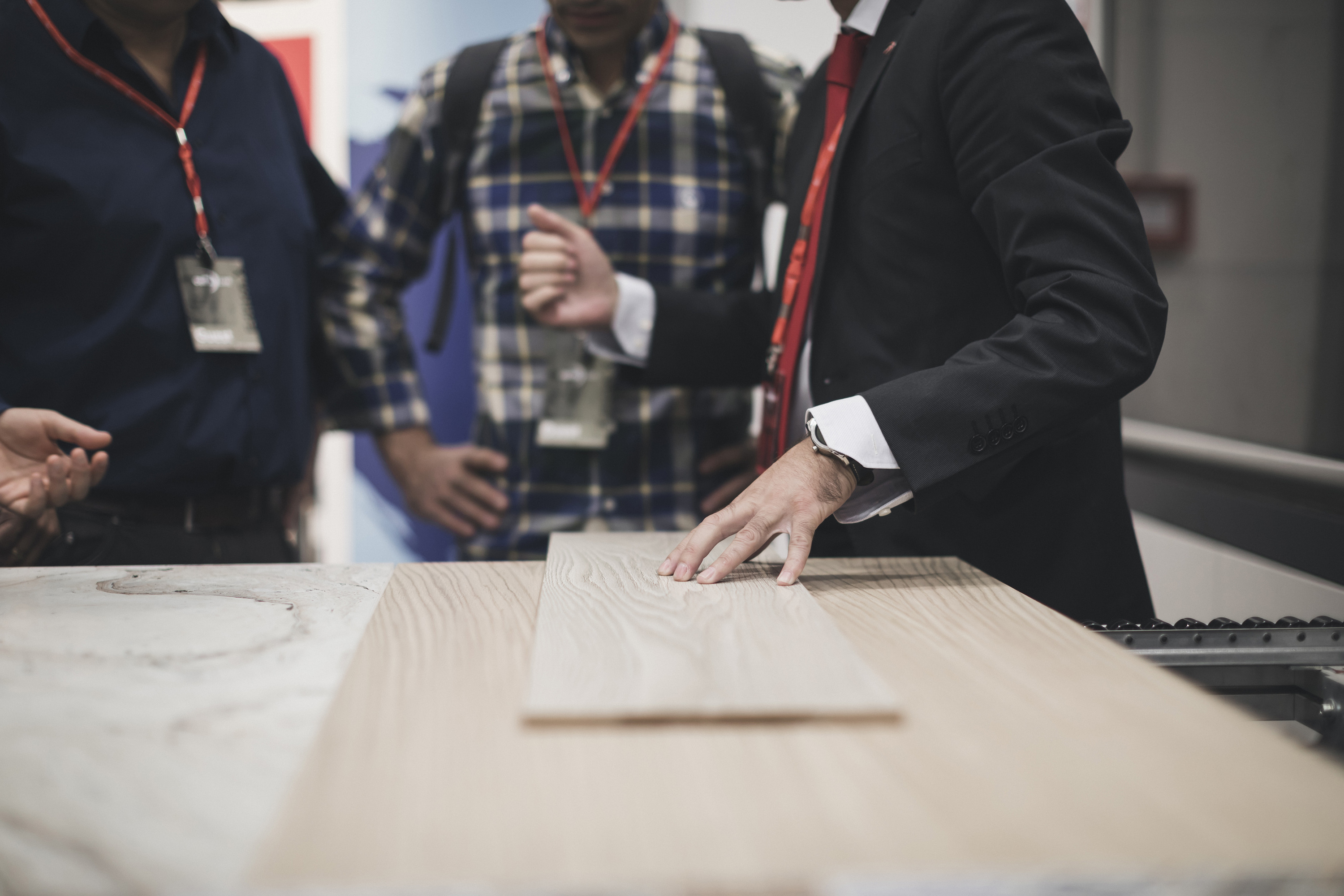
Connect
Frequently Asked Questions
Frequently Asked Questions
Examples of products suitable for roller coating:
- cabinet doors
- parquet
- doors
- wood and wood-based materials
- glass
- cork
- plastic
- fibre cement
- metal
- roll-to-roll for edges etc.
High flexibility in terms of output rate and choice of cycles/processes according to the line make-up.
Zero solvent emissions thanks to 95% use of products with high dry residue (UV) content.
Possibility of using the roller technique for any application on all flat surfaces.