A solution for the coating of musical instruments needs to carefully consider aspects which include shape and substrate, but also the priorities a customer has regarding lacquer, aspect, productivity and, above all, the acoustic quality once the manufacturing process is terminated. Our team has assessed all variables and we have developed custom-built finishing lines for harps, pianos and other musical instruments.
A musical instrument is often made up of many different parts, large – think of a grand piano – or small and made of both wood and metal such as a harp’s components: neck, body, soundboard, base and column, all of which form the frame. Many of these components require multiple layers of coating, sanding operations and special treatments.
Intervals between coating phases are strictly regulated as well as the application parameters. Often temperature excursions affect the quality of the process, but most of the inconsistencies come from the fact that a great deal of the process is entirely manual. Automation would bring a number of benefits…
Why automation solves the principal issues facing a manufacturer
In several cases that we have handled, the crucial issue involved a part of the process that was accomplished manually. This frequently meant moving large or small pieces from one area of the workshop to another entailing physical fatigue and disrupting workflow. It also led inevitably to severe contamination issues which can only compromise the characteristics and quality of a musical instrument.
How automation transforms the process and enhances quality
- controlled timing of the process
- controlled process environment
- consistent coating performance
Harps
Salvi Harps, based in Italy’s Piedmont region, needed to move from a manual to an automated coating process. Mainly with the intention of drastically reducing the handling operations which added no final value to the product, the aim was also to achieve greater control over coating parameters.
Pianos
Fazioli has been making high-quality pianos since 1981. Crafted at their facilities in the town of Sacile, north east of Venice, the company produces around 150 pianos per year. According to 'The Economist', Fazioli, a company that 40 years ago did not even exist, is today considered a virtuous example for its commitment to research, renewal and product enhancement: a piano that always looks to the future. Our role in innovating their coating process contributed to the overall quality of the product and improved productivity.
Cajones
Located in a small town in southern Germany there is a renowned company that has been producing Cajones since 1982. Originally hand-crafted by the men who founded the company, in 2003 production moved to a larger factory premises. This percussion instrument evolved into a variety of models and aesthetically it expressed different identities. Keen to increase efficiency and gain total control over the coating process, the company approached us to bring the finishing operations from a third party outfit back to their own facilities.
Tailored solutions are possible drawing from a range with so many different technologies
Thanks to a vast selection of finishing solutions and a 3000 sqm laboratory where we can experiment and develop customised equipment, our process specialists can adapt each technology to the majority of customer-specific requirements. Much more than a standard wooden panel, we have developed integrated lines for glasses, helmets, musical instruments, solar panels, motor vehicle dashboards, ceramic slabs, almost anything.
Projects
We have helped hundreds of companies around the world achieve their quality, efficiency, and productivity goals. Here are their stories.
We have helped hundreds of companies around the world achieve their quality, efficiency, and productivity goals. Here are their stories.
Do you want more information?
Please contact one of our experts.
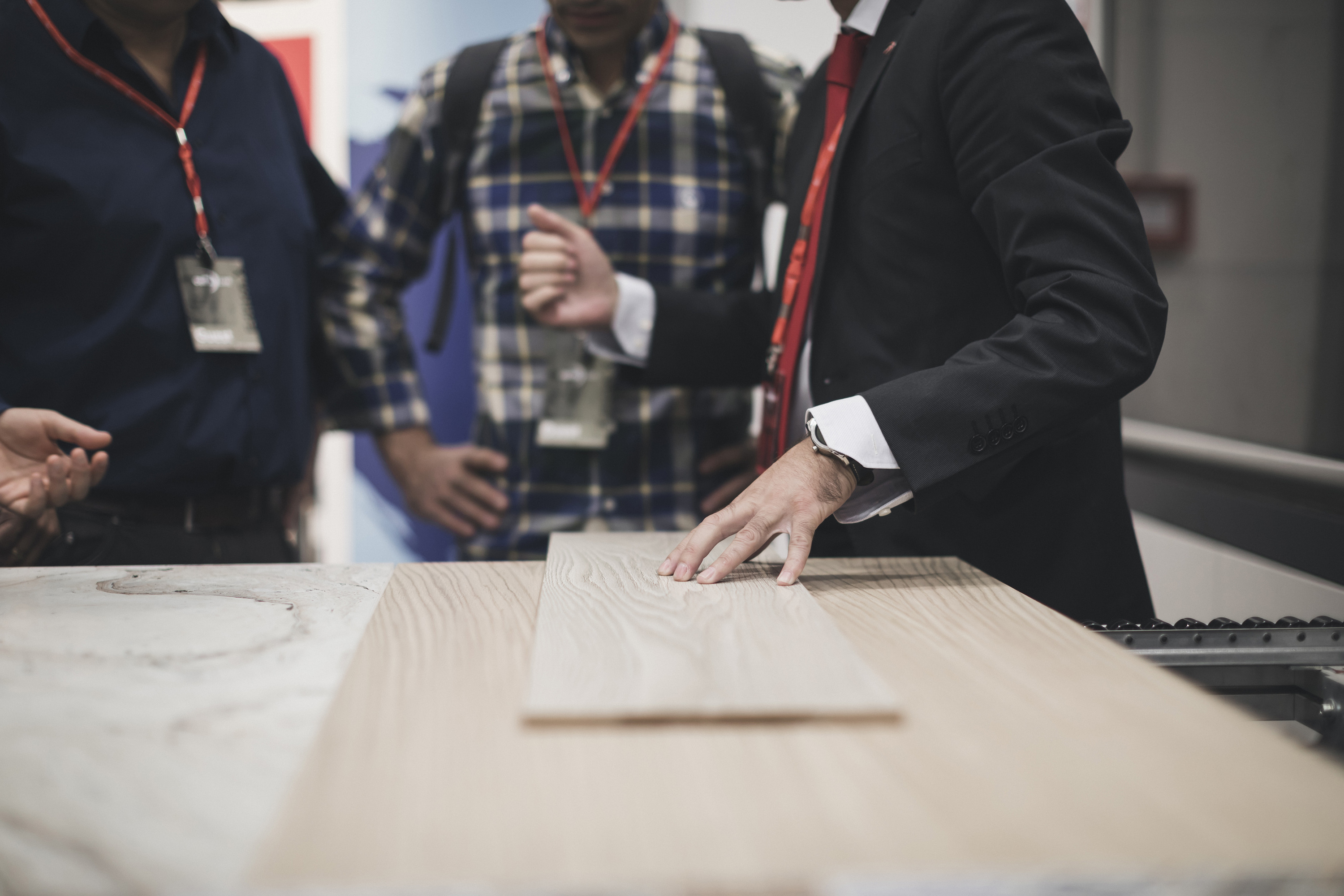
Connect