
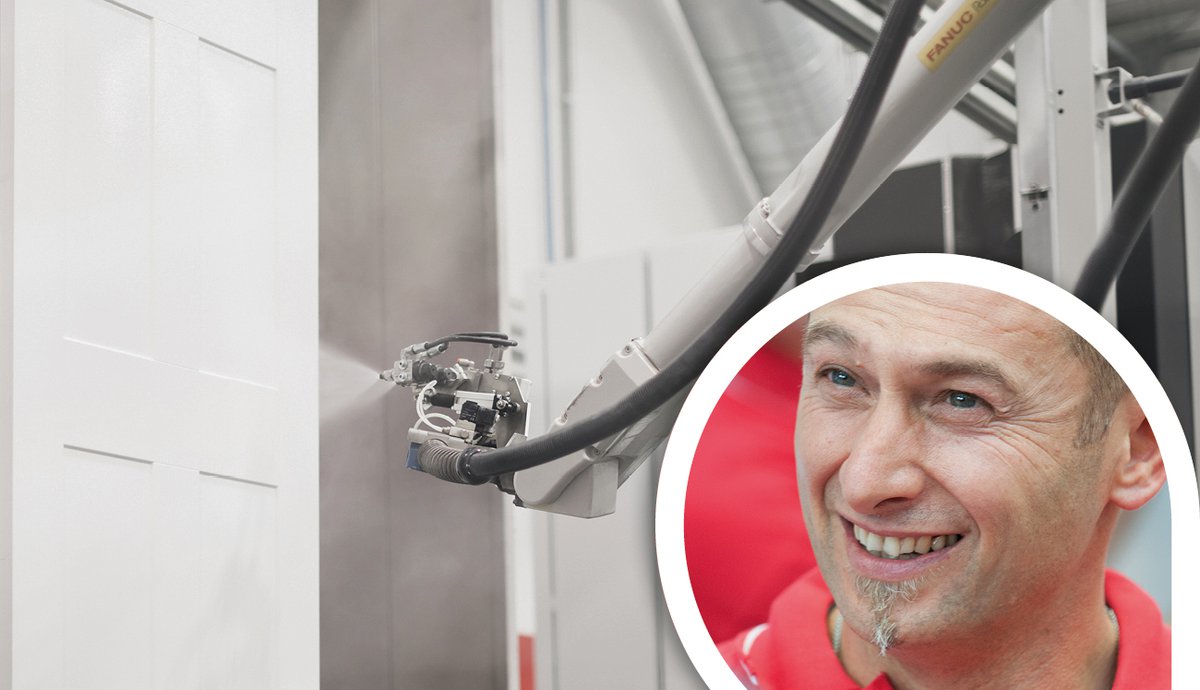
The main difference concerns piece management.
If, on the one hand, certain start-up concepts remain valid (e.g. spray gun positioning, loading the coating, cleaning procedures as with oscillating sprayers), on the other there is a substantial difference in the way the parts are coated as it's possible to spray three-dimensional objects of various kinds.
With oscillating spray coating machines, just turning a selector switch may be sufficient; with robot spray coating machines, instead, the operator creates a specific job recipe for the product to be processed on the machine control PC. Today, this task is made simple by several optional systems, scanners and classifiers that ensure the machine can recognise the piece and automatically activate the correct work sequence.
➜ Let's talk about 2D and 3D systems: what's the difference?
The 2D system allows for calculation of piece thickness, longitudinal tilt and vertical tilt so that the most suitable coating programme can be selected. This system ensures homogeneous coating quantities over the entire product.
The latest-generation, automatic 3D reading system (cVision) allows acquisition of the position, size and shape of transiting pieces with unprecedented precision.
➜ What are the advantages?
Time savings, coating savings, quality and flexibility. The combined action of laser and ultra-high resolution cameras lets iGiotto, for example, completely and automatically generate precise work trajectories based on the object "families" in its database.
Eduard Raffini
LAB Application Manager
Test specialist and Coordinator of the Cefla Finishing HQ LAB