
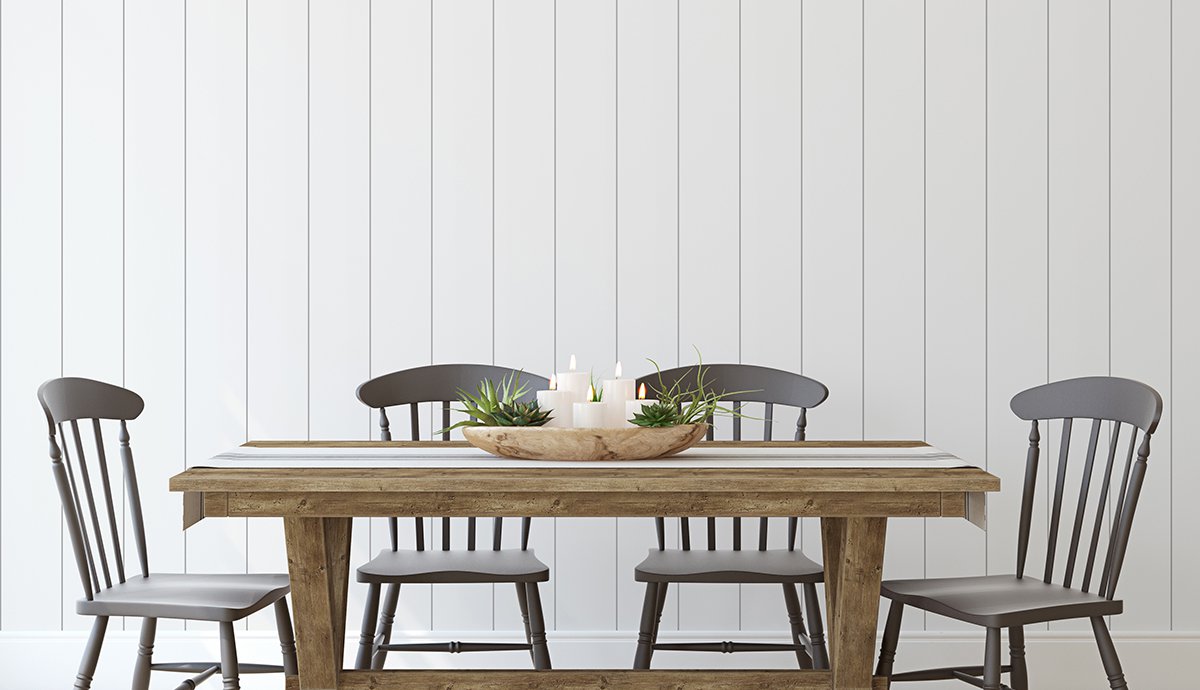
Vacuum technology is a finishing process that can coat either three or four sides of a profile or linear board and minimizes VOC’s (volatile organic compounds) that negatively affect the ozone. The technology minimizes the amount of wasted coating by continuously recirculating coatings through the system onto parts as they are fed through the system. The application head has a manual adjustment feature that allows the coating thickness to be controlled as it is applied to each part. This feature is typically set before production starts or is included in your product’s “formula.” By way of a 12-inch wide conveyor, the parts automatically exit the application head and enter into the curing or drying unit.
Cefla’s vacuum units are compact, multi-process painting systems. Depending on model, specification and application, systems include sanding, staining/priming/coating, and curing/drying units that allow parts to easily integrate from a secondary process, to finishing, to a finished good ready for shipping – with minimal human interaction. Cefla has Vacuum Finishing Systems for both water-based and 100% solids, for UV, finishing needs.
The CVR and CVS Vacuum Finishing Systems have maximum working widths of 8- to 12-inches and minimum working length of 24 inches, making it ideal for optimizing the production of linear profiles and flat boards including shiplap, which is growing in popularity in North America due to its feature on several DIY and reality television shows. Using vacuum technology, shiplap can be denibbed, coated, and cured or dried in a single pass, then packed and shipped.
Other system features:
- Low VOC’s for minimized emissions
- Closed loop system offers maximum transfer efficiency
- Small footprint
- One system comprised of multiple processes – no need for different sets of equipment
- Options for water-based and 100% solid UV coatings
- Machine-side control panel is easy to use with a touch screen featuring large print and color graphics
- Compatible with wood, wood-based derivatives, plastic, and metal substrate
- Made in the USA
These machines are designed exclusively to support the needs of a variety of North American industries, including residential and commercial construction. Contact us today.