
What is UV curing and what advantages does it provide in the delicate drying phases - essentially important to complete product finishing processes? The first consideration to make is that - regardless of the type of lacquer to be applied and the items to be processed (flat or raised panels, or panel edges) - new curing solutions keep appearing on the market, based on fast-evolving innovative technologies.
Understanding which winning combination could help you build the most efficient curing system to suit your needs - based on the substrates to be treated, your type of process and your production volumes - is essential in order to maximise the advantages offered by the new machines.
LED technologies
An analysis of the current curing scenario can only begin by mentioning LED technologies, which are playing an increasingly leading role in UV curing processes. After their introduction, LEDs have rapidly gained ground in several industrial applications, replacing traditional systems based on gallium or mercury lamps.
Some industry players are particularly interested in the opportunities offered by UV LED lamps. However, the general market has not yet fully grasped the potential benefits of LED technologies. These can offer significant advantages, particularly to companies active in specific areas:
- Panel finishing companies willing to invest in a new integrated finishing line, or to replace old UV ovens equipped with mercury or gallium lamps.
- Edge coating businesses interested in adopting LED UV technologies.
- Companies that use industrial digital printers, a segment in which LED technologies are already widely used for the pinning and final drying phases.
LED UV Curing: main advantages
Obviously, each one of the three applications mentioned above has specific requirements, but it is still possible to identify a number of common benefits:
- improved sustainability
- operating costs reduced to a fraction
- safety and flexibility
- control over process stability
- long lamp life and minimal maintenance requirements
Differences between traditional UV and LED curing
Going into more detail, there are five factors underlying the clear superiority of LED curing compared to curing with traditional lamps. Let's review them:
1. Ultraviolet light source
In traditional UV curing, the lamps require a warm-up period and have a relatively short lifespan, requiring more frequent replacements.
LED UV curing uses light-emitting diodes specifically designed to emit UV light, typically in the UV-A range. LEDs turn on and off instantly, providing instant curing without needing any warm-up time. They also last longer and are much less energy-intensive.
2. Energy efficiency and environmental impact
Traditional UV curing is not only more energy-intensive but also requires the disposal of hazardous materials, resulting in environmental risks. Additionally, traditional lamps will expose the coated films (and consequently, the substrates) to considerable heating.
LED systems are more energy efficient, as they convert a greater amount of electrical energy into usable UV light and will produce less heat. This level of efficiency reduces energy costs and improves sustainability by minimising the carbon footprint associated with curing processes.
3. Material compatibility
In traditional UV curing, the broader light spectrum emitted by mercury vapour lamps can cure a wide variety of product formulations, including some that might not work well with narrower UV wavelengths. However, this versatility comes at the cost of increased heating, which can limit the types of substrates that can be used.
While if LED curing is compatible with a limited range of materials designed to respond to specific wavelengths, advances in product formulations are continually expanding the range of resins and coatings that can be cured.
4. Cost management
The initial investment needed for mercury vapour UV curing systems is lower. However, this cost tends to increase due to maintenance and lamp replacement requirements and increased energy consumption.
LED systems tend to have a higher initial cost, but long-term energy savings, low maintenance needs and longer life often make them a more economical option over time.
THE MOST INNOVATIVE FINISHING SOLUTIONS
Discover how highly advanced finishing solutions can enhance your competitiveness.
Common issues in UV curing (and solutions provided by LED technology)
The differences listed here above lead to very different outcomes when it comes to the effectiveness and efficiency of production lines. First of all, it is impossible to achieve the required curing process stability with mercury lamps without having to frequently measure their intensity and constantly monitor their operation. This often leads to downtime and loss of production capacity. Additionally, a mercury lamp has a life span of 1500/2000 hours, while an LED lamp lasts approximately 30,000 hours without suffering any significant UV intensity losses.
Panel overheating caused by traditional UV lamps should also be considered. MDF panels and resinous woods are significantly affected, as they can exude resin at high temperatures. UV LED lamps, by contrast, are much cooler and have no adverse effects on these substrates.
And what about environmental sustainability? Disposing of mercury lamps requires a lot of red tape in addition to causing ecological concerns (the RoHS directive prohibits mercury lamps for home use, and this rule could easily be extended, in the future, to industrial applications), and UV LED lamps are so much easier to handle in terms of separate waste collection.
As mentioned, standard UV lamps are energy-intensive (which also increases production costs and makes setting up lines difficult wherever the energy supply is insufficient). UV LED lamps' consumption is between 50 and 60% lower than traditional systems based on mercury lamps.
As we mentioned before, cooling systems are required for mercury lamps and they release ozone, which is conveyed out of the facility via an air-cooling system. All this has economic and environmental costs, especially for large production sites, which could partially be avoided with UV LED technology.
UV LED Curing: a modern and sustainable technology
The aspect that ultimately tips the balance in favour of UV LED technology is technological innovation. A UV LED curing system is managed electronically, which means that only the actually required lamps are switched on, also setting the exact intensity needed. The UV LED lamps send information to the PLC, allowing system managers to achieve significant savings on energy costs. This makes the process truly sustainable from an ecological and economic point of view.
As mentioned above, a UV LED system requires virtually zero maintenance. The lamps last approximately 30,000 hours and without interruptions, production efficiency is boosted allowing for non-stop processing without any downtime and ensuring constant quality levels over time.
Why switch to UV LED lamps?
In a market scenario that is increasingly interested in UV LED curing techniques, the strategic elements in favour of this technology are mainly:
SUSTAINABILITY – operating and environmental safety is a key issue for future business success.
ADAPTABILITY – thanks to a wide and constantly evolving range of solutions, machinery manufacturers can now effectively customise their proposed solutions.
Cefla's expertise made available to companies looking for innovation
Cefla Finishing installed its first UV LED oven back in 2014, and has therefore been able to acquire and analyse technology-specific data for many years. With an installed base of around 200 units between wood panel coating lines and digital printers, the experience we have acquired to date is second to none in today's marketplace.
As a partner of Phoseon Technology, leading manufacturer based in Oregon, we can share our expertise based on 120,000 systems sold so far and 300 technology-specific patents. This makes our offer extremely flexible, but also allows us to provide consulting services based on our solid knowledge of different use cases and above all, on our systematic analysis of the data generated by countless implementations.
After all, this has always been Cefla Finishing's approach: listening to customers, understanding their business objectives and defining the most appropriate solution based on the key factors involved:
- environmental
- economic
- performance/production-related
The range developed over the years is so wide that it allows us to select the right UV LED lamps from a pool of different models, with different wavelengths and dimensions - catering for every need.
In particular, our UV-R LED ovens can be integrated into three types of lines:
- panel coating (new or retrofit solutions)
- panel coating incorporating excimer ovens
- industrial digital printing
Find out how we can help you make your business more efficient and innovative.
LOOKING FOR THE IDEAL COATING LINE SOLUTION?
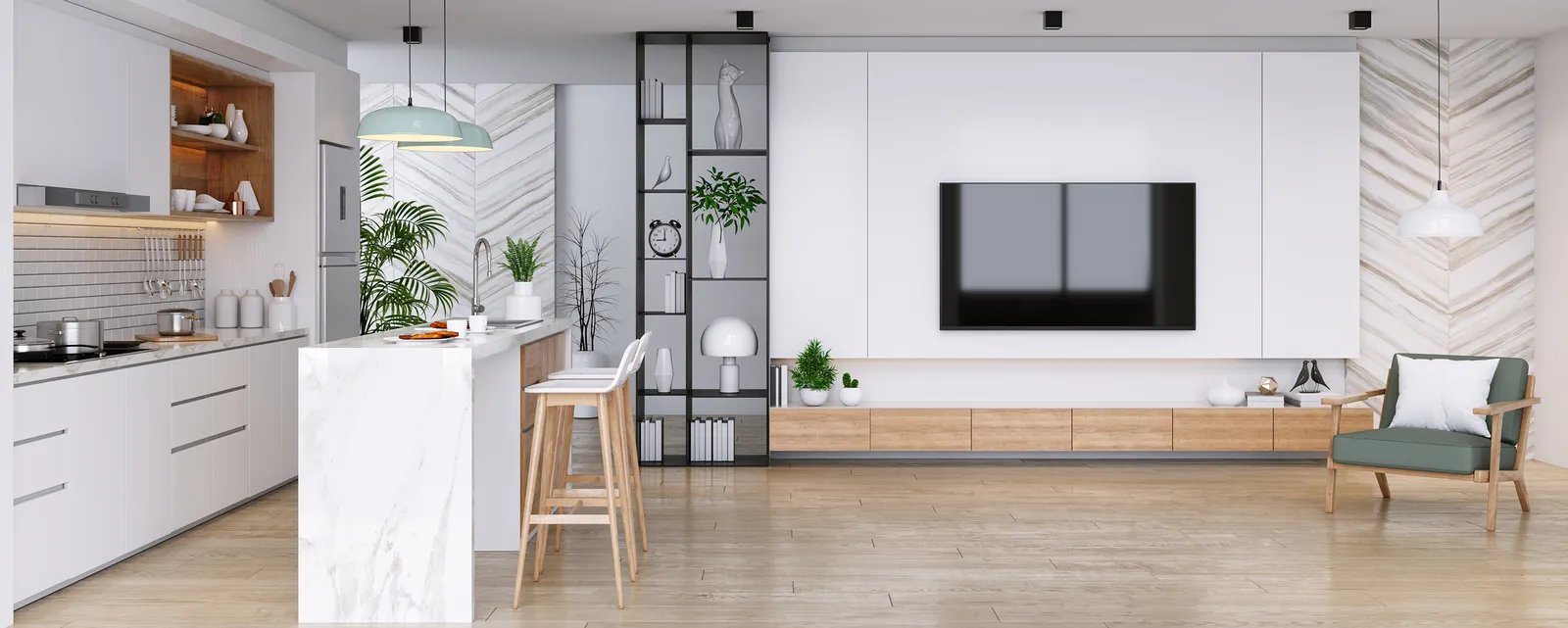