More and more, terracotta flower vases are being replaced by plastic vases.
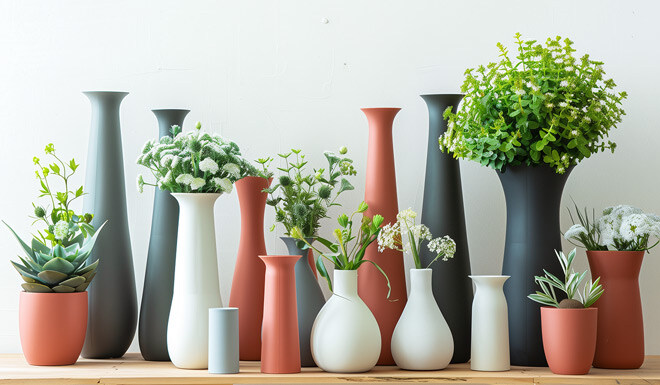
At first glance they might seem like simple objects, but they nevertheless require production processes that are anything but simple. Market operators engaged in the finishing of plastic objects know this only too well.
This article refers to manufacturing contexts, to those companies that make or finish the vases. It also refers to the many companies involved in processing three-dimensional objects that work within a wide range of sectors.
The best vase coating solution
To obtain objects with impeccable aesthetic and surface performance, nothing must be left to chance in the vase coating process.
With years of experience in finishing, in numerous industries and with a broad range of materials, we’ve had the opportunity to test a wide range of solutions. Through this experience, we’ve now identified the most efficient, effective way of producing great, high-quality vase decoration while minimising the manual workload.
This is spray coating: a finishing line technology that allows for customised use and configuration.
Spray-coating: the perfect vase coating solution
Let's now look at the ‘made in Cefla’ spray-coating line set-up. One possible solution sees a line that includes a high-performance articulated robot, such as iGiotto. The vases in question are attached to rotating swivel pins that slide along a floor-mounted line.
The vase coating process
Stage 1: flaming
Stage 2: spraying
Stage 3: drying
Customisation of finishing lines
In addition to these advantages, it’s possible to customise every aspect of the line to meet customers’ specific needs, whether they’ve already established a process and simply wish to improve it, or whether they’re still looking to identify the solution that best suits their business.