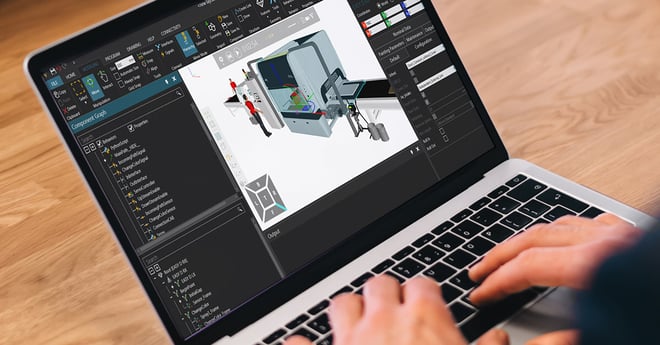
The expression “production process” contains a key concept related to business management and, more generally, modern economy. It is the set of procedures, activities and skills involved in the processing of raw materials into finished goods and services.
What is a production process?
According to its most exact definition, the production process – or production cycle – is a method by which inputs (raw materials, labour, technology and capital) are turned into outputs, i.e. products and services. There are different production logics: one is based on orders, another one on batches, one is mass-based and another one is continuous; each one is characterised by different phases, going from the initial idea of a product to its design, all the way to actual implementation and delivery of the output package to the end consumer. It follows that understanding how each stage works and incrementally identifying areas for improvement is essential for organisations seeking to optimise business efficiency, reduce costs, and meet customer requests.
Let's see in more detail, before analysing the approaches that can help improve overall management, what the different phases of the production cycle consist of.
Planning and design
The process starts with brainstorming sessions for the creation of new products and services or for the improvement of existing ones. The activity includes market research to focus on consumer needs, feasibility studies and prototype creation.
Procurement
Once the project is finalised, the next step is to purchase the necessary raw materials and components. This phase often involves negotiating with suppliers, assessing quality, and handling logistical challenges.
Production
The next step is the actual production phase. Depending on the nature of each product, there may be different production chain set-ups: the choice of the most suitable one impacts both process efficiency and output quality.
Quality Control
During the production cycle, companies implement quality control measures to ensure that products meet specific standards. Let's review the inspection, testing and regulatory compliance processes.
Packaging
After production, the products must be carefully packaged for distribution. The purpose of packaging is not only to protect goods, but also to play a critical role in marketing and branding.
Distribution
The final phase consists in delivering the finished products to retailers or directly to consumers. This involves managing logistics, inventory and transportation to ensure that products are available wherever and whenever they are needed.
THE MOST INNOVATIVE FINISHING SOLUTIONS
Discover how highly advanced finishing solutions can elevate your competitiveness.
Production process improvement
The matter is extremely complex - as all those working in the field are well aware of. However, not everyone is aware of the fact that analysing the data generated in each of phases listed above can significantly improve the production process.
A data-centric strategy, especially if implemented within a modular and flexible technological environment, results in greater efficiency, lower costs and improved product quality, enabling organisations to make informed decisions, even in real time, to proactively respond to critical issues, or to anticipate problems before they even occur. Organisations that adopt data analytics systems are also better positioned to adapt to changes and improve production capacity even in times of crisis.
Data analysis, however, is only the first step on the way to smart manufacturing. Today, companies can use simulation models that provide a “digital twin” of new or existing production scenarios by feeding to them data generated by existing processes (we will see an example below). This makes it possible to consider the adoption of different strategies and identify optimal workflows before implementing changes in actual practice.
The same approach can be applied to people management. Data analysis and simulation development help assess employee productivity and performance, identifying areas where staff may need additional training or support, and also improving shift scheduling. The result is twofold: labour costs are reduced and employee satisfaction is increased.
Finally, by evaluating customer preferences and feedback, a data-centric strategy allows companies to adapt their production processes in order to better meet requests and drive product development so as to responds to market trends and fill any gaps.
Optimisation of production processes
When performed correctly, these activities can help plan specifically targeted actions able to streamline costing policies related to labour, materials, and overheads - thereby increasing profitability.
A well-defined manufacturing process includes quality control measures, ensuring that the end product is up to the required standards while reducing waste. Fine-tuning these procedures can also lead to a significant improvement in the available offering.
A clear understanding of the production process allows companies to adapt their lines to changes in consumer demand, technology and market conditions, helping smoother supply chain management, improving inventory management and shortening delivery times.
Finally, optimising the production cycle is an essentially important choice for companies that aim to minimise possible bottlenecks in the supply chain, to cope with periods characterised by a shortage of qualified workforce and to comply with regulatory frameworks, which, given the increasingly stringent requirements in terms of environmental sustainability, may require significant investments.
Tools for production process simulation: cCloner
How do you carry out, in actual practice, a simulation of the industrial production process and use it to make your process evolve to achieve your business objectives? Cefla Finishing has created cCloner, a line simulator with several advanced features designed to improve each phase of the production cycle and respond to specific market needs.
More specifically, the solution:
- shows a realistic 3D configuration of the line layout, delivering an effective, reliable picture based on measurements, 3D imaging and objective data.
- simulates real line operation. In this way, as early as in the design phase, it is possible to prevent critical issues, avoid machine downtime, and obtain more general information.
- highlights actual productivity and helps identify the best line configuration.
The real strength of cCloner lies in its ability to offer a holistic view of the plant make-up and production process functioning: if used systematically, the software helps to configure each section, thus ensuring that the value chain as a whole complies with production requirements.
Companies that adopt a solution like the one designed by Cefla Finishing can therefore develop skills to not only minimise inefficiencies along the line, but also predict the ROI for plant upgrades.
LOOKING FOR THE IDEAL SOLUTION FOR YOUR COATING LINE?