
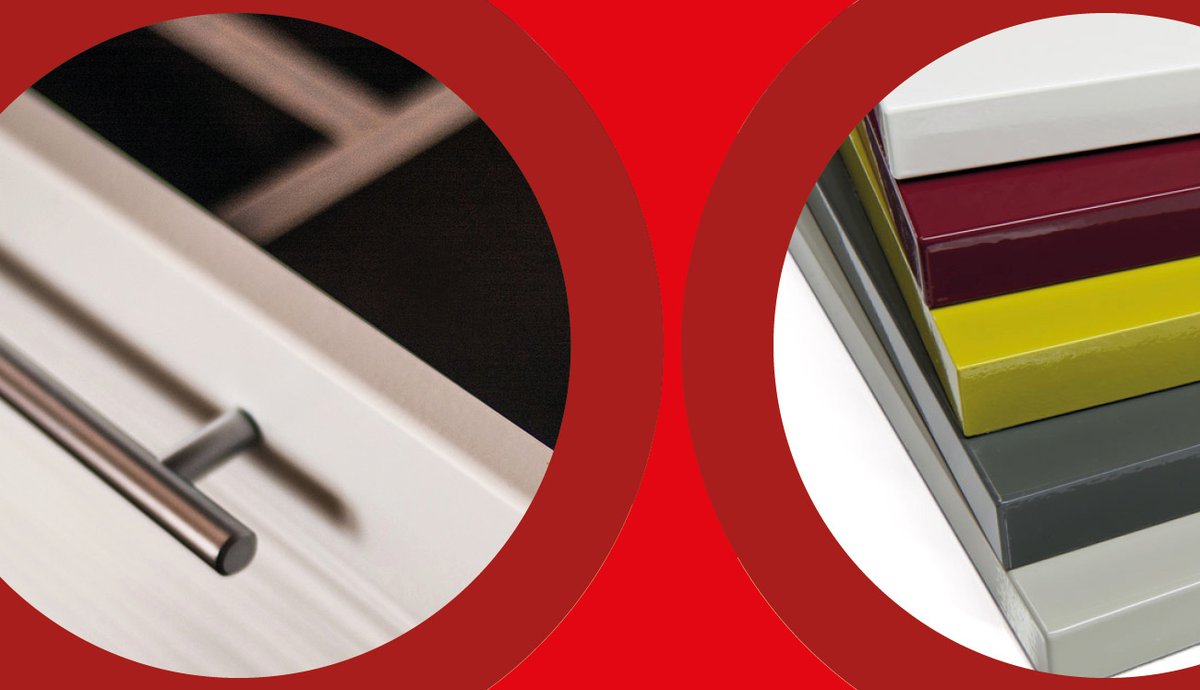
Approximately 80% of today’s kitchen cabinet doors or bathroom cabinet doors are no longer raised panels, but simple, smooth flat panels with slightly rounded edges. Essential design, which deserves high-quality coating, especially when matching the edge coating with the surface coating.
But why introduce vacuum coating technologies when the market is used to roller coating, spray coating or curtain coating? Let’s take a look at the reasons behind this innovation.
Which application are we talking about?
Ideal for 100% UV basecoats, vacuum coating with SmartVacuum deposits 100/140g / sqm of lacquer in a single step. Much less than what you would consume if you were spray coating. No solvents either, so just one stage in and out of the vacuum coater and on to flash off. This reduces costs, lead time and streamlines the coating process.
Where next?
Straight on to the edge coater. SmartEdge will then apply 100% UV lacquer to the panel’s edge using vacuum coating technology once more, achieving an excellent match between panel surface and panel edge, something which was almost impossible until now. Currently edges are slightly rounded, with a 2-3 mm radius usually; vacuum coating both sections increases panel quality and decreases process times and costs.
Sustainability also saves money
On one hand, the idea behind SmartVacuum is a means of lessening the environmental impact by preferring solid 100% UV coatings to avoid solvents. On the other hand, this positively impacts costs. Less lacquer: far less compared to spray coating, and depending on which process it is compared to. It also means less need to stock all those canisters of lacquer and solvent. It also means fewer machines: one SmartVacuum and oven to flash off followed by one SmartEdge for application on the edges.
Simplicity also means quality
By simplifying the process, the introduction of vacuum technology to coat flat panels and edges leads to superior quality. Using the same technique for both surface and edge clearly enables a perfect match which is immediately visible. Moreover, the stability of UV lacquers is better than those used currently, so the quality finish obtained will also last much longer.
If you are interested in learning more about the potential SmartVacuum offers for flat panel coating requirements, we will advise you on the best configuration and choice of consumables, based around your specific needs and business objectives. Contact us today.
Roberto Sorbini
Business Line Manager | Roller Coating Technologies
Product development, technologies and machines for roller coating