
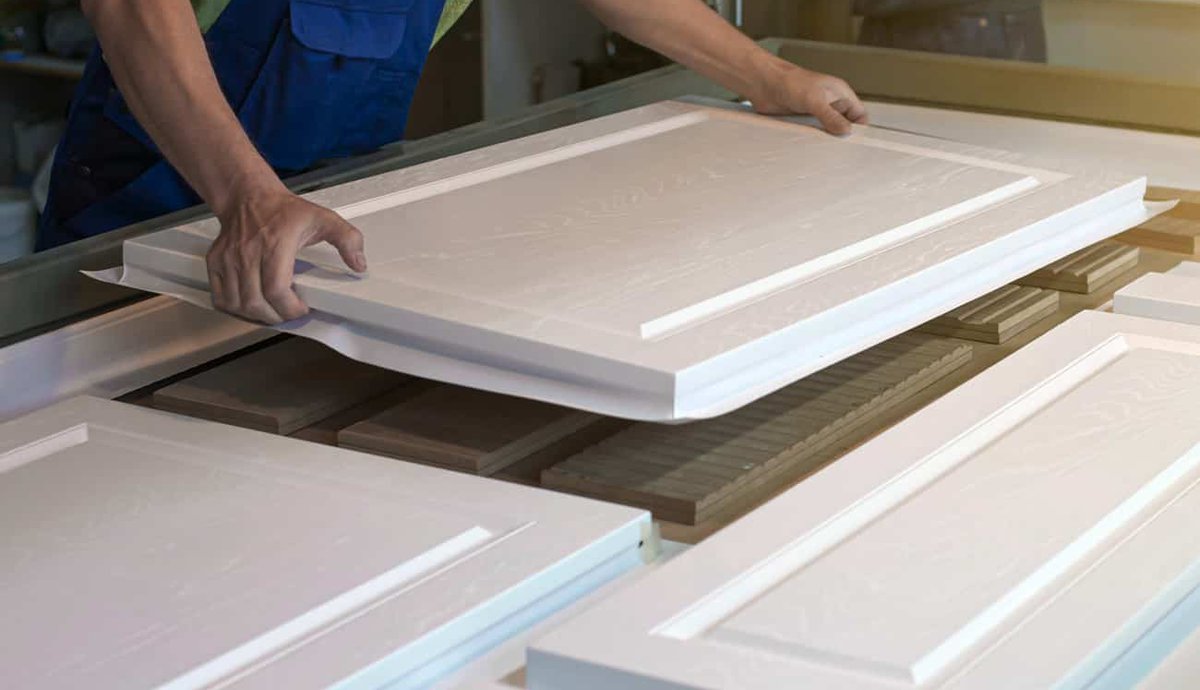
Application of PVC foils is one technique that necessitates the use of glue, and glue is by no means the easiest substance to handle. Uniformity of application is a key issue across the surface to avoid defects once the foil is applied. This is just one focus point, whereas an integrated line will address many different issues from loading to offcut disposal. Let’s take a look at each step.
Turning the step-by-step process into a smooth, integrated workflow
Automated solutions for panel loading reduce manual operations right from the start. Subsequently the panels are brushed on Smartclean to obtain a smooth surface. Applying glue to flat surfaces can be done using a Mito. This is a great way to move from manual activity to an automated solution. To maximise productivity and also apply the glue to edges without soiling the reverse side of the panel, we advise iBotic, our 5-axis application robot. Benefits include excellent application consistency, repeatability, operator health as well as all-round precision. The water content needs to evaporate from the glue and after using a Mito just for the flat surface, we would advise Aquadry, whereas Pieffe will be a better solution ensuring superior productivity if application to surface and edges was performed on an iBotic.
The PVC foil is then applied on a press (third party equipment). The last two stages involve trimming the excess foil, shredding it and disposing of it. We have a solution for both: Tarcut ensures greater efficiency and precision, especially when fitted with a 3D camera, while Twister takes care of shredding scrap foil and disposing of it, so it can be recycled.
Each customer will require the appropriate configuration, incorporating one or more of these machines in an integrated solution, able to feed any number of presses.
Contact us and discuss your needs with a finishing expert.