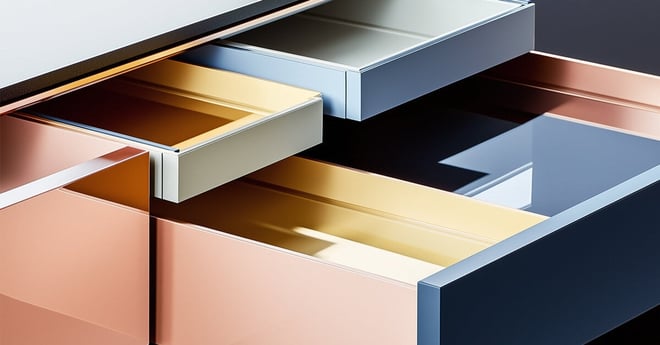
Edge coating machines are playing an increasingly crucial role on panel construction and finishing lines. The market is, in fact, striving to respond to fast-changing trends that are fuelled by strong demand for customisation (just think of the automotive sector): this explains why orders for small batches are becoming more commonplace, and only those who hone their capacity to process semi-finished products - especially their edges - flexibly will manage to retain their competitiveness. Consequently, edge coating and sanding machines must not only ensure optimal processing regardless of the material or type of finish requested by the customer: they must also make it easier to perform the frequent format changeovers intrinsic to customisation in order to avoid bottlenecks and unprofitable downtime.
What are the requisites for top-level edge coating machines?
Because of the refinement and complexity of the parts requiring intervention, it’s simply a fact that edge processing influences the entire panel coating process: that’s why outstanding edge coating machine performance is vital to improving and speeding up production. Machines must be efficient to manage large-scale production, flexible to provide just-in-time capabilities and hyper-precise to ensure consistent quality that matches the panel finish.
And it’s no coincidence that our customers ask us - ever-more insistently - if we can provide systems that let them achieve a good balance between processing speed and cost containment, but without compromising performance. Our response? It’s called Smartedge.
EDGE COATING
Discover how to solve edge processing problems
Smartedge: applications and advantages
Smartedge is the ultimate edge coating machine. Featuring integrated functions, it doesn’t just ensure high-performance, low-consumption edge coating, filling and sanding: because it’s configurable, with specific modules designed to meet every quality and productivity requirement, the solution also delivers outstanding flexibility.
Coatings can be applied with either a traditional vertical roller or a patented soft vertical roller, which automatically models itself to the shape of the edge without the aid of counter-templates. You can also choose to use vacuum injection technology, a Cefla Finishing patent that lets you coat any type of edge. How? By using an applicator head that’s contoured perfectly over the edge to be treated, ensuring precise, uniform coating whatever the shape of the piece.
Lastly, drying takes place in an integrated oven: UV (for 100% acrylic paints) or IR (for water or solvent-based products).
Smartedge can be configured to work with all types of edge, improving application consistency, reducing the need for specialised labour and preventing solvent emissions thanks to the exclusive use of 100% acrylic UV products.
Innovative edge processing with Edge&Go
For the most demanding clients, Cefla Finishing provides Edge&Go, our vacuum technology with applicator head that revolutionises the traditional approach to edge processing and edge coating machine control.
Normally, dismantling the applicator head and realigning the components to match the size and shape of the metal profile require a lot of time. Edge&Go is an integral part of Smartedge. By allowing continuous processing of different edges, it boosts productivity and maintains excellent coating quality while allowing workers to manage different edge shapes and sizes in the shortest time possible.
As the saying goes, time is money: that's why managing shape changeovers with Edge&Go (which can switch from straight edges with a 3 mm radius to J-Pull handle edges in less than 15 seconds) generates tangible, measurable economic savings.
A special (patented) dual applicator head with skimmer is now available; installed between the two coating dispensers, the skimmer acts as a filler, sealing all the micro-holes that might be in the MDF substrate. Each edge coating station can apply from 150 to 180g/m2.
Cefla Finishing, the perfect partner for better edge processing
To see Edge&Go and all the different technologies that make our profiling machine range one of the most advanced on the market, simply visit us at the Cefla Finishing Lab. Featuring more than a hundred Cefla Finishing machines, this technology hub is designed to impart experience, generate business goals and enable new opportunities by allowing for the creation and testing of entire processes and production lines. And there's more: visiting the Cefla Finishing Lab also provides great opportunities for identifying the most suitable case-specific configuration parameters and calculating the ROI for each machine.
If you need to reduce edge finishing costs and times, come and see the technologies and services that offer just what you’re looking for: our experts are at your disposal to assess and customise every single solution.
LOOKING FOR THE IDEAL COATING LINE SOLUTION?