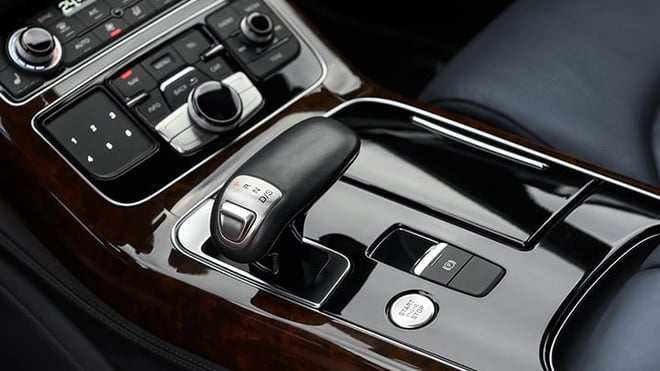
How to select the right type of finish
Choosing the right finish for the various types of automotive component means taking into consideration a wide range of factors: the material used to make the part, the setting it’s likely to be used in, plus the technical and aesthetic requirements of the vehicle on which it’s fitted.
Hence the need for a partner who does not have an excessively vertical approach to the functional-technological aspects of finishing processes but, rather, one who also knows how to assess the aims of the process and come up with properly tailored solutions.
Finishing technologies for automotive components
Of course, the technologies themselves are fundamental. However, to obtain an excellent result it’s equally essential to know how best to combine them according to the type of material to be treated and, above all, the component to be produced. That’s why Cefla Finishing goes beyond the design and development of efficient, precision machines to focus on consultancy.
For example, we provided a German customer - who needed to set up a new coating line as part of their car dashboard/console production process - with a solution tailored to their stated needs: the components produced by the new line would have to be completely defect-free as, once ready, they would be shipped directly to the vehicle assembly lines.
To deliver the required performance, then, the line was configured as follows:
- Line loading with manual cleaning and air-jet/deionization
- Cleaning with CO2 and air-jet/deionization
- Spray coating with Cartesian robot
- Lacquer flow, flash-off
- IR and UV oven for first drying
- Vertical oven for final drying
- Line unloading and quality control
Automotive component production: the materials used in finishing
High-precision machines need to be matched with top-quality materials. Hence Cefla Finishing’s entry into strategic partnerships with the major lacquer and coating suppliers.
Thanks to an in-depth understanding of consumables and their characteristics, solutions provided to customers can be configured to optimise both the consumption and yield of the materials. In automotive component production, that means:
- Lacquers (water-based and solvent-based): resin and pigment-based, available in different finishes and colours
- Primers: used to improve adhesion of the lacquer to the surface of the component
- Anti-rust coatings: to protect components from corrosion
- Lubricant coatings: to reduce friction and wear
Future trends in automotive component finishing
This is the present. But what about the future of automotive component finishing? Well, one of the key trends in the sector is the use of low-bake lacquers, which can be dried at lower temperatures than their traditional counterparts. To be specific, about 80/90 °C as opposed to 140/160 °C.
Specialised producers of automotive components are also increasingly focused on systems that automate the coating process, such as systems with robotic stations that use dry-type lacquer filtration mechanisms.
Market developments aside, one thing is certain: companies operating in this extremely competitive sector must always ensure their customers - car makers - can count on productivity, quality and efficiency.
And that’s where flatbed systems - a Cefla-developed solution for the ultra-efficient finishing of automotive components - come into play.
Advantages of flatbed systems
But how do flatbed systems differ from traditional lines? The latter tend to be the right choice when you need to coat large 3D parts: bumpers are a good example of an item best treated using these lines.
However, when items are smaller (up to 30 cm high), flat lines, or flatbeds, are decidedly more flexible and efficient. The technology is therefore particularly suitable for vehicle interiors, which have numerous components that require a high-quality process.
The flatbed lines implemented by Cefla Finishing include a robotic system with a scanner to detect pieces that involve minimal programming. Each booth can host up to two different robots. This boosts the processing speed or the coating circuit, with users able to select between intelligent or continuous spraying, depending on the shape of the objects.
Flatbed lines can handle different, even mixed, parts on simplified masks: such masks only need to be rectangular with a flat frame and, of course, they need to hold the parts in position. This approach also makes manual cleaning faster and simpler during loading and quality control.
Note also that this is a modular system (also available with cTracker and cLink line supervision software): it can easily be expanded by adding other standard machines without having to make any substantial modifications. Yet another reason, then, why flatbed lines maximise conveyance flexibility: there's no need for step movements as on traditional lines because each machine can act independently.
Adopting a flatbed solution provides tangible, measurable advantages:
- Compact operation, resulting in less consumption and reduced exhaust air flow
- An easier-to-manage process, with consequent labour and energy savings
- Lower cost per coated part
Why choose Cefla Finishing to optimise automotive component production?
The automotive component manufacturing sector is constantly evolving: technology is progressing at a blistering pace, with digitalization paving the way for new, innovative finishing solutions.
Nevertheless, we’re still talking about a complex, delicate process that is crucial to vehicle quality and performance: so nothing can be left to chance. This is why it’s vital to team up with a technological partner with skills that go beyond the technology itself: a partner able to deliver high-performance products, continuous innovation, expert assistance and a commitment to joint research and development. That partner is Cefla Finishing.
If you’d like to see what we can do for your business, and experience the effectiveness of our solutions for yourself, contact us: we’ll put you in touch with one of our experts.
LOOKING FOR THE IDEAL SOLUTION FOR YOUR COATING LINE?