A solution that goes into orbit
Project Data
Customer:
Avio SpA
Country:
Italy
Media Video:
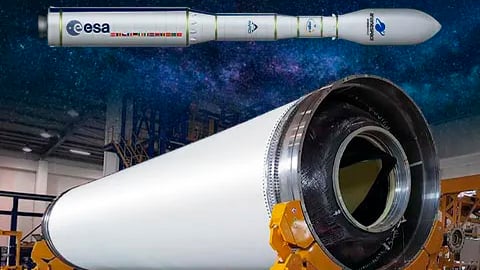
For AVIO - an Italian company that designs and builds satellite launch vehicles - Cefla Finishing has demonstrated its ability to achieve extremely challenging goals in terms of precision, productivity and consistently repeatable quality: three key factors that led to selection of the proposed solution.
One of the most important materials used in the aerospace industry on satellite launch vehicles is the outer heat shield. This has the vital task of protecting the launch vehicle structure from the high temperatures generated by friction with the air during the stages of atmospheric supersonic flight. To this end, thanks to its lightness and great insulating qualities, cork is used, in sheets of different thickness; these sheets are used to line the outer surfaces of the carbon fibre launch vehicles.
Moreover, to ensure electrical continuity of the vehicle and so prevent any build-up of electrostatic charge on the components, all external heat shielding has to be coated with a special anti-static paint to offset the very low conductivity of cork.
The first specialized process for painting the cork lining was manual, and had all the limitations typical of any manual technology: in this case, the main drawbacks were non-uniform thickness of the paint layer on the various sheets, inconsistent raw material consumption and non-optimized cycle times.
To achieve higher quality and productivity standards and allow industrialization of the process, AVIO began looking for an automated solution.
A big boost to productivity with the Cefla Finishing solution
The paint - applied automatically with iGiotto App - is a special resin that combines the required electrical conductivity with incredible strength. Primer and resin can be applied both on flat sheets and three-dimensional parts using iGiotto App, which guarantees a constant basis weight and allows the company to produce more flexibly.
The second part of the selected solution boosts line productivity further. The Omnidry oven has been sized to meet daily production requirements and, because it can adapt to the transiting pieces, has provided greater flexibility. After the primer has dried, the material automatically returns to the iGiotto App for application of the resin, the process being completed by the end of the work shift.
By switching to an automated solution, the customer now has perfect control of the basis weight and enjoys consistent final product quality. This milestone has allowed attainment of the desired conductivity parameter and a 30% reduction in resin consumption. As the resin is particularly expensive, these quantity savings have also yielded considerable economic benefits.
Automation also means fewer staff are needed on the line. Today, the entire cycle can be overseen by just two people while achieving, compared to the past, a fivefold increase in productivity.
Further advantages take the form of traceability throughout the entire process, which is essential as each batch has to be certified. To this end, cTracker now gives the company perfect control over finished pieces thanks the continuous tracking of each individual processed load. Monitoring, control and logging of system parameters - such as the applied basis weight, temperature and the time in the oven - are associated with the individual batch and allow the entire process to be certified.
In addition to proposing technologies designed to ensure an error-free process, the ability to run test cycles at the Imola LAB proved to be a key factor in the customer’s decision to select Cefla Finishing.
The photo shows the casing of the P120C engine, the first stage of the new Vega-C launch vehicle (inaugural flight 13th July 2022) and the side booster on the future Ariane 6 launch vehicle, both part of the ESA (European Space Agency) launch vehicle family. All the painted external heat shielding is clearly visible on the casing (this explains the typical white appearance of launch vehicle exteriors)